Rotary Dryer
Basically, we have two kinds of designs of rotary dryer: Triple layer drum dryer and single layer drum dryer. Depending on the project requirements, we can give the best solution.
1. Triple Layer Drum Dryer
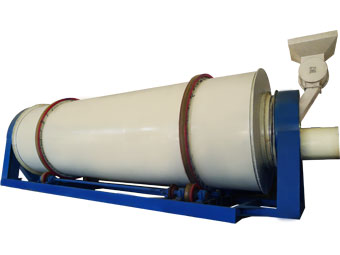
Application Scope
The triple layer drum dryer is an energy-saving and high efficiency drying equipment. It can process not only high moisture content material with low viscosity,but also high viscosity material. The dryer is applicable to dewatering all kinds of mash and residues with water content less than 85%, such as brewery mash, wood sawdust, alcohol mash, fruit residue, poultry dung, litter, etc. It has a good effect on exploring new feed resource, reducing the raising cost, and lessening environmental pollution.
Mechanical Structure And Operating Principle
The wet material is fed by feed device to the inner layer of the dryer where forward flow drying is realized. The material is repeatedly shoveled and dispersed by the lifting plate to do heat exchange in screw movement forward. Then the material moves to another end of the inner layer and enters the middle layer, where counter flow drying is realized. And the material is winnowed repeatedly and makes its way two steps forward and one back. During this period, the material can fully absorb the heat given by both the inner and middle layers. And at the same time the drying time is extended,which can make the material perfectly dried.
The material moves to the other end of the middle layer and falls into the outer layer,where the material makes its way in the form of rectangle multiple chains, and the dried material moves faster,then will be discharged out of the drum dryer in the same direction with the airflow. The wet material will still stay inside and being dried until it’s dry enough.
Main Advantages
- To reach the same capacity, triple layer drum dryer occupy less space. Its overall size is less. Easy for transportation and installation.
- Sufficient in heat exchange: the heat exchange between the material and the hot air is realized by reciprocal and cross motion in the direction of forward flow, counter flow and again forward flow, with long time of heat exchange. The moisture evaporated from the material in the inner layer is directly exhausted by the fan. Therefore the heat utilization rate is high.
2. Single Layer Drum Dryer
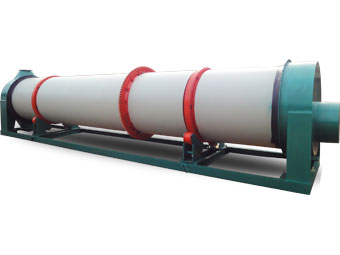
The rotary dryer is the choice for high throughput capacity applications, involving high moisture, friable, free-flowing materials, etc. A rotating drum and strategically positioned flights combine to lift and shower product evenly through the air stream.
Thermostatically controlled discharge air temperature assures precise final moisture and allows sensitivity to varying product conditions.
We also have extinguish system and anti-explosion system on our dryer.
Structure of single layer drum dryer is not so complex as triple layer design. After the wet material is taken into the dryer through inlet, it is turned over by the string-up rake inside the drum and distributed uniformly in the dryer for full contact with the counter-current hot air. It speeds up the heating and mass drying process. While drying, raw material is moved by stirring rake with a gradient of hot air. It passes through the drying region to a star valve which discharges the dry material.
Technical Parameters
Model | Diameter (mm) | Length(m) | Power(kw) | Speed of rotation (r/min) |
HZG6 | 600 | 4,5,6,7,8 | 3-5.5 | 3-20 adjustment |
HZG8 | 800 | 4,5,6,7,8,9,10 | 5.5-7.5 | |
HZG10 | 1000 | 6,7,8,9,10,11,12 | 5.5-7.5 | |
HZG12 | 1200 | 6,8,10,12,14,16 | 7.5-11 | |
HZG15 | 1500 | 8,10,12,14,16,18 | 11-15 | |
HZG18 | 1800 | 8,10,12,14,16,18,20 | 15-18.5 | |
HZG22 | 2200 | 10,12,14,16,18,20,22,25 | 18.5-22 | |
HZG24 | 2400 | 12,14,16,18,20,22,25 | 22-30 |
Design specification for SIMEC dryr’s saftey operation:
-
Anti explosion
Our design is to use the rupture disk to prevent the damage of dryer in case of explosion or pressure rise. Below there’s a sample image for the rupture disk.
The rupture disk is suitable for gas media. In case of explosion, there’s no sparks, no sharp pieces.
On the rupture disk there’re holes and cracks to reduce the strength. When the protection system is overpressure, the rupture disk will break along the cracks and holes to release pressure. Rupture disk will be connected with L type pipes. In this case, the air flow direction will be changed. - Sprinklers (in the first part of the dryer) to allow for prompt stoppage of self-combustion of material.
Automatic Sprinkler for Fire-Prevention in Drying System
Function: quick start in case of self-combustion of material and extinguish the fire.
The alarm & auto-sprinkler system should be equipped in front end of drying drum in order to improve safety performance of drying system, and prevent fire.
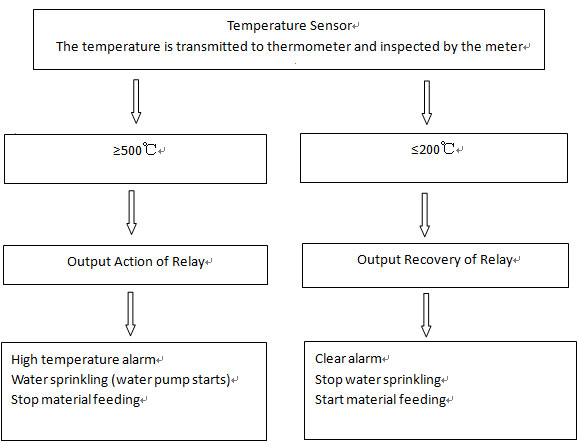
Main Parts List
S/N | Part Name | Model | Q’ty |
1 | Intermediate Replay | AC220V | 5pcs |
2 | Knob | Diameter 22 | 1pcs |
3 | Indicator Light | Diameter 22 AC220V | 1pcs |
4 | Acousto-optic Alarm | AC220V | 1pcs |
5 | Temperature Sensor | Platinum Thermistor Pt100 | 1pcs |
6 | Thermometer | TZ4M | 1pcs |
7 | Circuit Breaker | DZ108-20/211 | 1pcs |
8 | AC Contactor | AC220V | 1pcs |
9 | Water Pump | 1set | |
10 | Water Pipeline | 1set | |
11 | Cable | ||
12 | Sensor Signal Line |
-
After confirmation of contract, and before manufacturing, the drawings including sizes will be worked out and confirmed by both parties.
The cables/bridges specifications will be provided before delivery of equipments. - Temperature display for inlet hot air and emission air.
- Moisture detector for wet material and dried material.
- Water spray dust collector for the complete drying plant. And the emission will be clean.
-
Sparks Settling Channel
Between the steel shell and fire bricks wall,there’s insulating layer for heat. To achieve effective elimination of sparks, we make the design to include sparks removing barriers. On every spark barrier, there’s one blow hole for air. The air holes are staggered up and down. So the airflow will move in the form of “S” wave.
Under every spark barrier, there’s a door to clean up the dropped spark ash. When the sparks impact the fire bricks,t hey’ll be killed and fall down, then become to be ash.
On every air hole, a filter screen will be installed. It’s made of 316 stainless steel that can work in high temperature. There’re two layers for each filter screen device.
The filter screen will stand on skidway which makes it easy to be disassembled. The skidway device is also made of 316 stainless steel. The filter screen device is fixed by screw on the wall of spark settling channel. The above is a brief presentation for SIMEC drying technology. We trust that the above proposal meets your requirement and please do not hesitate to contact us should you require further information.
Photos of rotary drum dryer
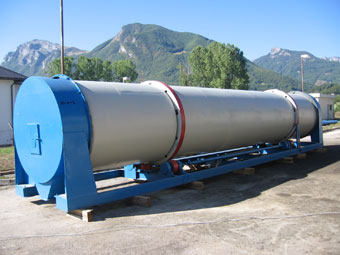
Rotary dryer before install
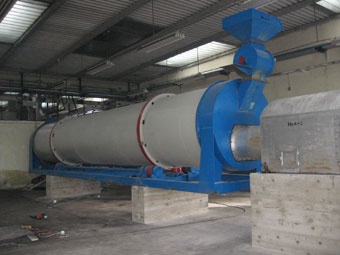
The Workshop of rotary drum dryer
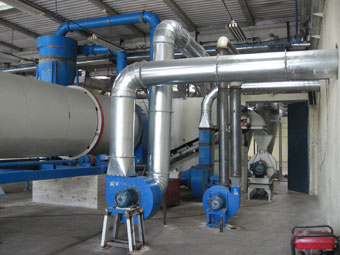
Rotary Dryer Pipelines