Use SIMEC Automatic Rotary Charcoal Furnace to Produce Quality Charcoal
Instead of producing charcoal by batch in traditional method, SIMEC charcoal furnace can achieve continuous quality charcoal producing. This entire plant requires only 2~3 operators. After start up the pyrolysis furnace, the worker only needs to feed biomass materials into the feeding hopper, about 20 minuets later, charcoal will be discharged from the discharger.
Recently, our Indonesian client who ordered one set of 1TPH Automatic Rotary Charcoal Furnace came and inspected the cargo. We are honored to do a test in our factory for the client. The raw material being tested are Rice Husk and Sawdust. In practical production in Indonesia, the raw material shall be Coconut shell.The Automatic Rotary Charcoal Furnace Test Video:
Please learn more about its delivery process at:
http://www.mobilepelletplant.com/news/automatic-rotary-carbonization-furnace-to-indonesia.html
Below is the text version of the test:
First of all, we need to pre-heat the drum of furnace by LPG. LPG Auxiliary Combustion Sys. is combined by LPG tanks,6 pieces of combustion terminals, LPG pipelines, air distribution devices and so on.
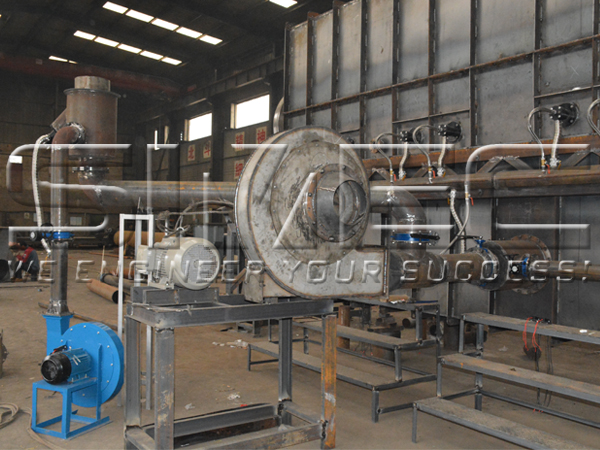
Air Distribution Sytem
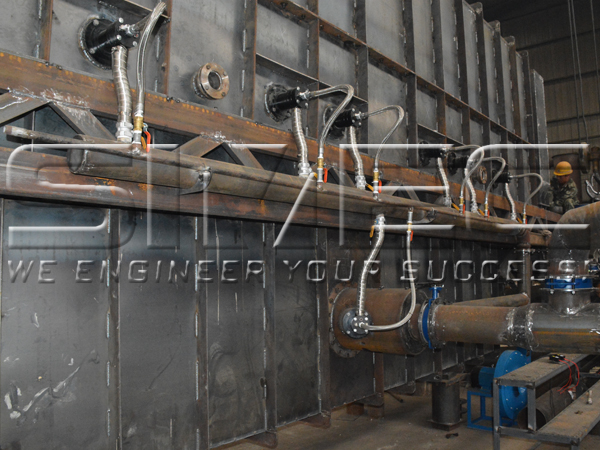
LPG Burning System
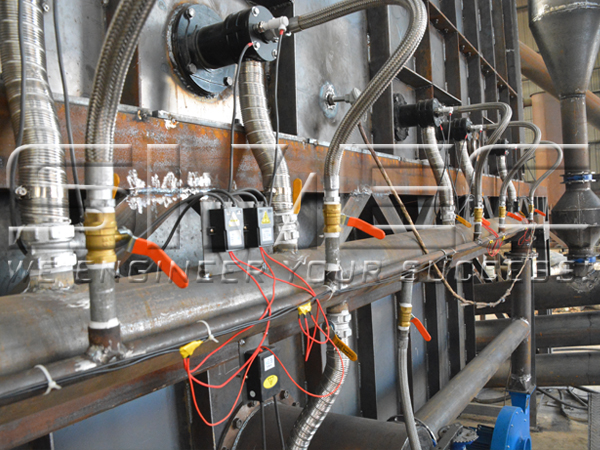
LPG Valves
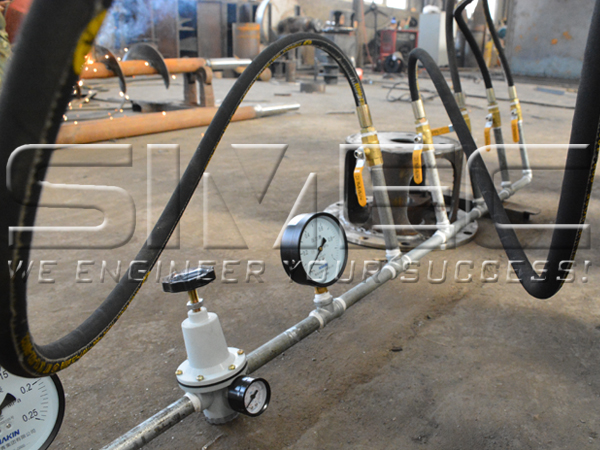
LPG Tubes
Distribution devices supply enough air for LPG ignition and combustion continuously. Ignition device adopts electric firing unit, fast and stable. There are individual valves to adjust the air flow of LPG to achieve proper combustion status. The proper temperature is able to reduce the moisture of the biomass raw material properly and generate moderate syngas from Light Carbonization process. Besides the combustion terminals, there are two viewports for observing combustion status of LPG.
Once LPG starts combustion, we can start up each machine of the entire plant one by one. One worker feed the raw materials into the elevating screw conveyor which has a feeding hopper. The elevating screw conveyor is interlocking controlled by the UPPER/LOWER level sensors of the buffer hopper above another screw feeder whose function is feed materials into the drums of furnace smoothly.
Once LPG starts combustion, we can start up each machine of the entire plant one by one. One worker feed the raw materials into the elevating screw conveyor which has a feeding hopper. The elevating screw conveyor is interlocking controlled by the UPPER/LOWER level sensors of the buffer hopper above another screw feeder whose function is feed materials into the drums of furnace smoothly.
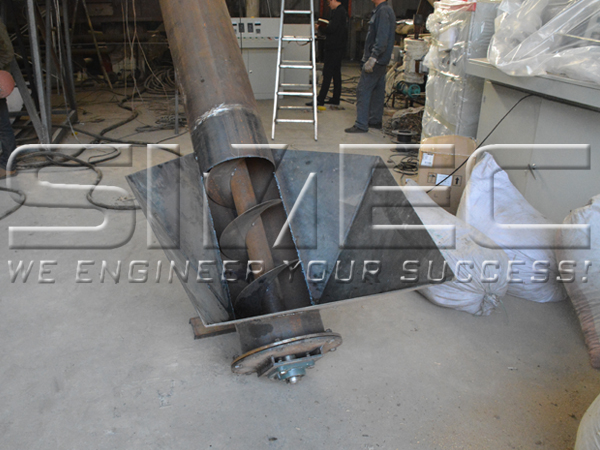
Screw Feeding Hopper
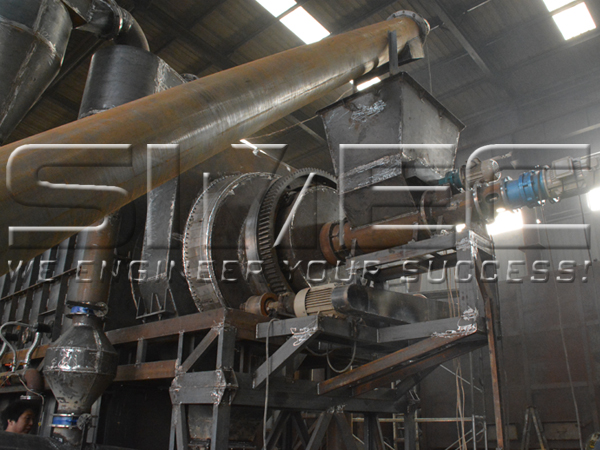
Screw Feeding Conveyor
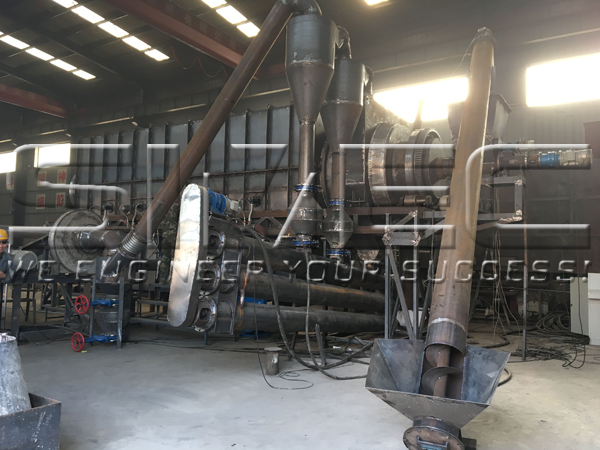
Feeding System
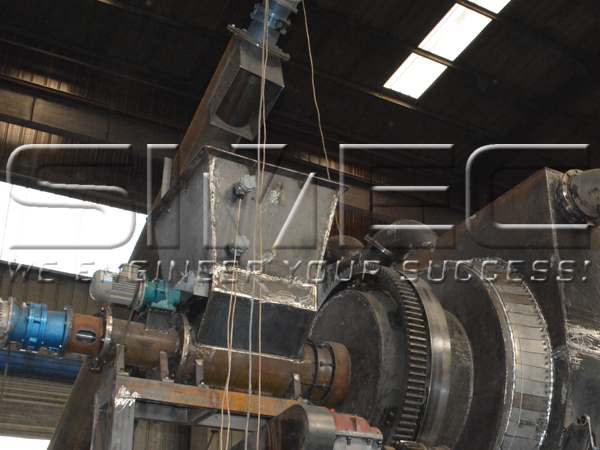
Feeding Hopper Level Indicators
So, when the materials in the buffer hopper reaches LOWER level sensor, the elevating screw conveyor start to feed the materials into the buffer hopper. Once the material reaches UPPER level sensor, it stops feeding. The screw feeder continuously feeds materials into the drum and consumes the raw materials inside the buffer hopper. When the level reaches LOWER level sensor again, the elevating screw conveyor starts work again, and so on alternately. The worker dose not need to feed the materials continuesly, but feed the hopper of elevating screw conveyor at beginning and refill it after some interval of time.
From indications of several devices of this plant, the operator can estimate the degree of actual process inside the drum properly.
There are two sets of temperature sensors of this plant. As we know, temperature is the most important index of carbonization process. And also, the driven motor of the drum is frequency controlled. The operator can adjust the inside temperature or raw material stay-time inside to achieve switching between different mode of production, such as Torrefaction, Middle level Carbonization and Complete Carbonization to meet kinds of requirements of final products from different clients.
There is also a tube which connects with a small water channel and the drum. The end of tube insert down to the water level of the channel. The air outside can’t get in from the tube but the inside air can go out through the water. It’s used to indicate the combustible syngas and also as the outlet of syngas in case of emergency. A simple design but very useful. Once there is bubbles come out from the tube, we know the carbonization process starts up normally.
From indications of several devices of this plant, the operator can estimate the degree of actual process inside the drum properly.
There are two sets of temperature sensors of this plant. As we know, temperature is the most important index of carbonization process. And also, the driven motor of the drum is frequency controlled. The operator can adjust the inside temperature or raw material stay-time inside to achieve switching between different mode of production, such as Torrefaction, Middle level Carbonization and Complete Carbonization to meet kinds of requirements of final products from different clients.
There is also a tube which connects with a small water channel and the drum. The end of tube insert down to the water level of the channel. The air outside can’t get in from the tube but the inside air can go out through the water. It’s used to indicate the combustible syngas and also as the outlet of syngas in case of emergency. A simple design but very useful. Once there is bubbles come out from the tube, we know the carbonization process starts up normally.
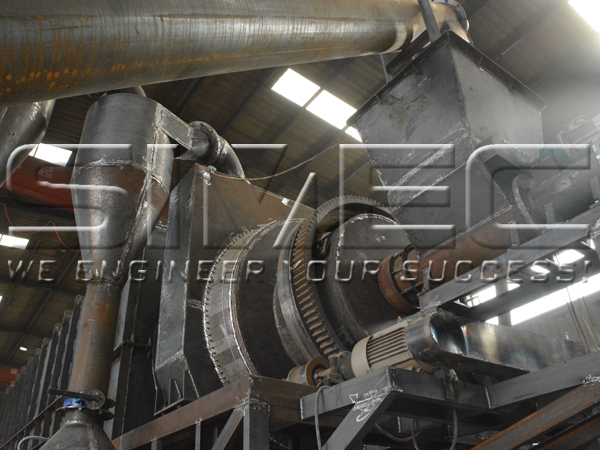
Reactor Drive System
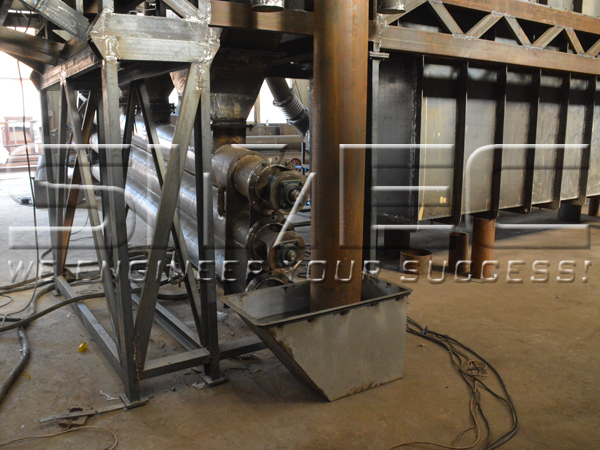
Gas Exhaust Tube and Water Pool
The combustion syngas is purified by cyclones before feed into Syngas Combustion Chamber. 99.9% solid impurities mixed are separated. And the tar and other liquid impurities stay in gas form under high temperature and will be burned completely in combustion chamber. It ensures there is no emissions to the atmosphere during production of entire plant. The blower of combustible syngas adopts stainless steel materials. It’s able to work stable under high temperature environment with long life span. There is also a view port at the side of the combustion chamber for observing combustion status inside.
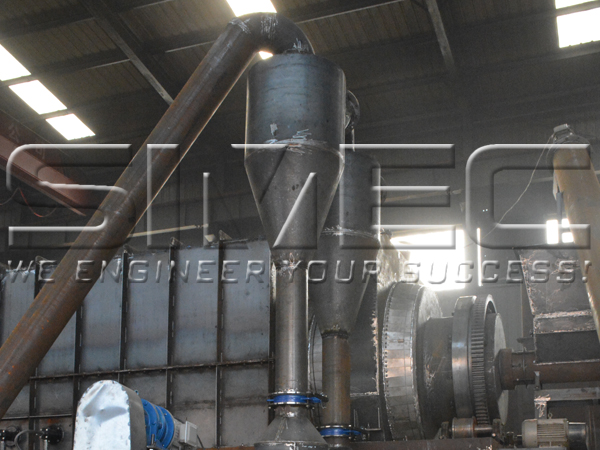
Cyclones
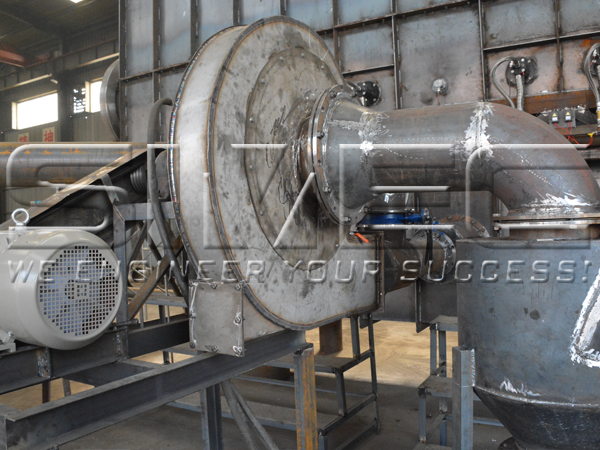
Stainless Steel Induced Draft Fan
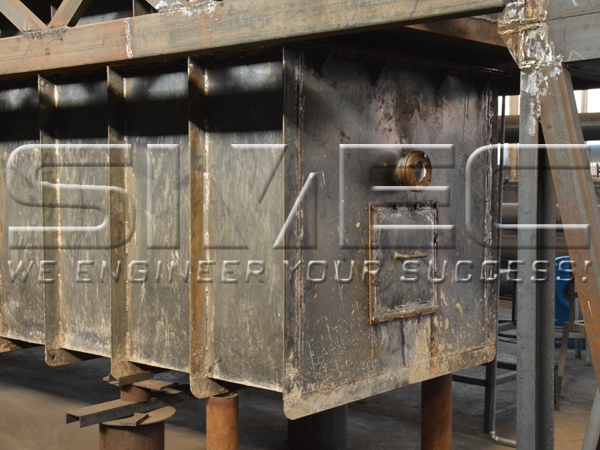
Gas Combustion Chamber
Thanks to the special design of charcoal screw discharger, we can get final charcoal with indoor temperature.
It’s three pass design with water cooling function which extends the cooling paths and performance extremely.
The water flow runs in the jecket of the wall and takes away the most heat of charcoal product. And there is water spray, which is able to add water inside the screw discharger directly to ensure that the final charcoal has no spark and with proper moisture for packing and long distance delivery. It’s customized based on the requirement of charcoal moisture of clients.
It’s three pass design with water cooling function which extends the cooling paths and performance extremely.
The water flow runs in the jecket of the wall and takes away the most heat of charcoal product. And there is water spray, which is able to add water inside the screw discharger directly to ensure that the final charcoal has no spark and with proper moisture for packing and long distance delivery. It’s customized based on the requirement of charcoal moisture of clients.
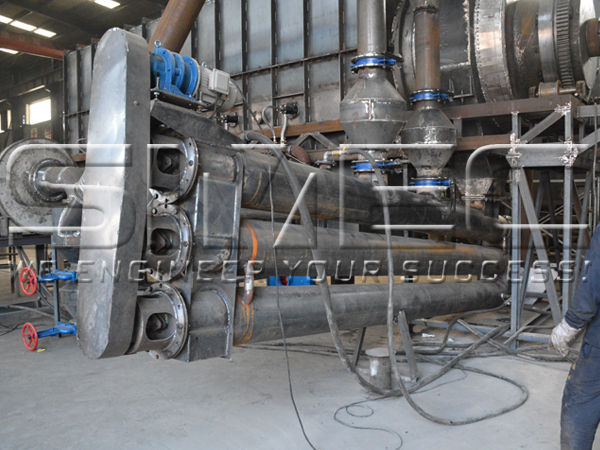
Triple Layer Discharger
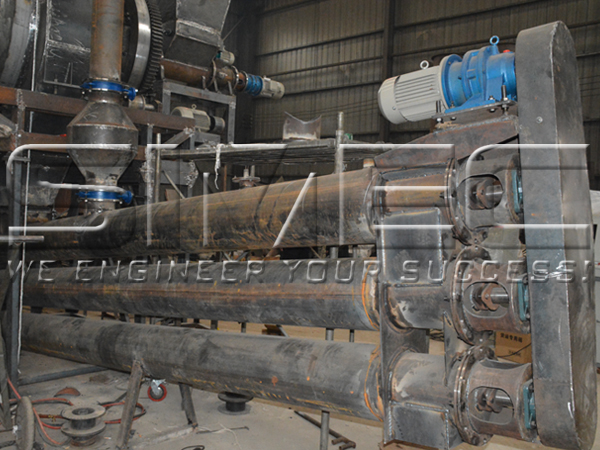
Triple Layer Charcoal Discharger
Henceforth, the biomass materials become quality charcoal products and output from the discharger endlessly. Our plant is designed for 24 hours production. So long as abundant materials supply, you can get the Black Fortune continuously. Would you like to try this easy operation and automatic rotary charcoal plant? Please feel free to contact with us.
We engineer your success!