Shutdown for Production Efficiency
As the increasing demand of wood pellets and affected by the great fluctuations of wood pellet price in South East Asian market from the end season in 2014 till to this first season, some investors in this area are inclined to establish big capacity wood pellet production line, and the small factories prefer the “apple-pie” pellet mill plant, that can operate by 24 hours x 30 days, to achieve fulfill capacity, so that they can get the stable purchasing orders. Nevertheless, to conduct the correct and scheduled maintenance is the safeguards of the effective production of the whole production line.
The last thing a pellet mill needs is a big-ticket item such as a rotary dryer or a drag chain to unexpectedly fail during the busy season, which can last from midsummer through early spring. Replacement parts may be backlogged and have to be shipped from overseas, meaning dollars are hemorrhaging from the plant in unfulfilled orders and idled capital equipment. One of our largest wood pellet production line located in Semarang, Indonesia, for instance, if they shut down for two days in the busy season, they are losing hundreds of thousands of dollars. That is a headache to most of the project owners.
This is precisely why plants big and small with rich operation experience plan the routine shutdown maintenance and a major outage at least once a year. It is so vital for the operational plants to get the most effective production. More routine maintenance procedures are performed during weekly, biweekly or monthly shutdowns. Whether it’s a weekly maintenance outage or an annual capital shutdown, the plant needs to be idled the same way. The major difference, however, is that a capital shutdown takes months of planning. Ultimately though, both short- and long-term outages help ensure equipment longevity, plant safety and production efficiency, keeping margins as robust as possible.
Most of our veteran clients conduct schedule routine maintenance from Friday through Sunday evening after the first shift operation. As the weekly shutdown approaches, it is conducted from emptying the equipment to shut down the whole line in order totally. For example, stop feeding the dryer, after all of the raw material is dried and conveyed out from the dryer, the operation team would cool down the burner and dryer system, and once those have cooled, all the material from the hammer mills have been pelleted. The equipment is then to be maintained.
For our customer who has the big factory, they would keep some equipment operation and shutdown others during the routine maintenance, and conduct the total shutdown biweekly during the busy season.
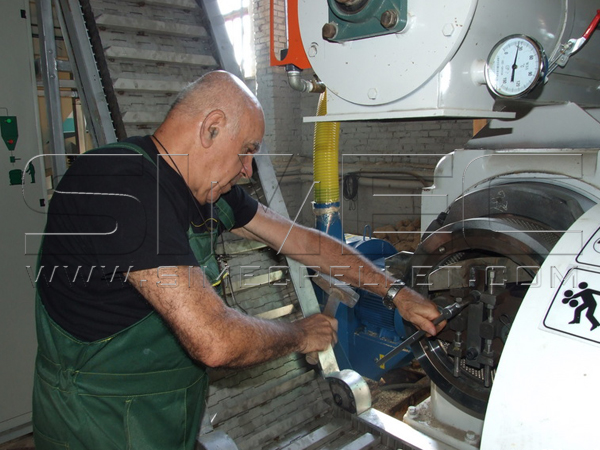
SIMEC Technician And Pellet Mill
Normally in a wood pellet production plant, after a production shift, the operator should inspect the gearbox oil, belt tensity, surface and holes of the ring die, roller shell, chain of the belt conveyor, lubrication to the roller bearings and main shaft bearings etc. Lubricating grease should be added sufficiently to the bearings before the next shift operation. After the daily production, raw materials in the ring die holes must be squeezed out by the oil raw material, which would prevent the holes from blocking when operate in the following days. Routine weekly or biweekly maintenance procedures range from changing gearbox oil, changing roller shells, and drilling ring die holes etc. Ring die replacement and other repairs can be conducted during the monthly shutdown maintenance. The time of the maintenance differs from the scale of the production line.
Anyhow, the longer a facility accumulates a history of operations with accurate, dependable tracking of hours, the more it can rely on predictive versus preventative maintenance. The veteran maintenance usually have a detailed maintaining schedule, so that they know clearly about the daily and weekly predictive maintenance and annually preventative maintenance.
Consider it ironic, but plants have to go down to be effective when they’re up. The most important qualifier to this is being in control of when the plant is down—avoiding having to shut down versus planning a shutdown. Despite the limit of the equipment, what you can do to improve the throughput is to conduct correct and regular maintenance, and accumulate rich operation experience.
The last thing a pellet mill needs is a big-ticket item such as a rotary dryer or a drag chain to unexpectedly fail during the busy season, which can last from midsummer through early spring. Replacement parts may be backlogged and have to be shipped from overseas, meaning dollars are hemorrhaging from the plant in unfulfilled orders and idled capital equipment. One of our largest wood pellet production line located in Semarang, Indonesia, for instance, if they shut down for two days in the busy season, they are losing hundreds of thousands of dollars. That is a headache to most of the project owners.
This is precisely why plants big and small with rich operation experience plan the routine shutdown maintenance and a major outage at least once a year. It is so vital for the operational plants to get the most effective production. More routine maintenance procedures are performed during weekly, biweekly or monthly shutdowns. Whether it’s a weekly maintenance outage or an annual capital shutdown, the plant needs to be idled the same way. The major difference, however, is that a capital shutdown takes months of planning. Ultimately though, both short- and long-term outages help ensure equipment longevity, plant safety and production efficiency, keeping margins as robust as possible.
Most of our veteran clients conduct schedule routine maintenance from Friday through Sunday evening after the first shift operation. As the weekly shutdown approaches, it is conducted from emptying the equipment to shut down the whole line in order totally. For example, stop feeding the dryer, after all of the raw material is dried and conveyed out from the dryer, the operation team would cool down the burner and dryer system, and once those have cooled, all the material from the hammer mills have been pelleted. The equipment is then to be maintained.
For our customer who has the big factory, they would keep some equipment operation and shutdown others during the routine maintenance, and conduct the total shutdown biweekly during the busy season.
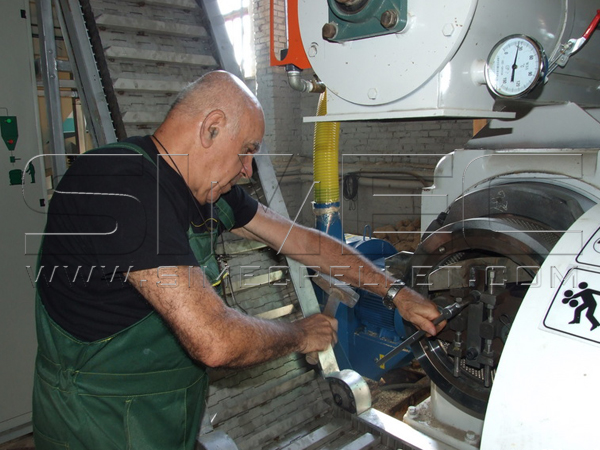
SIMEC Technician And Pellet Mill
Normally in a wood pellet production plant, after a production shift, the operator should inspect the gearbox oil, belt tensity, surface and holes of the ring die, roller shell, chain of the belt conveyor, lubrication to the roller bearings and main shaft bearings etc. Lubricating grease should be added sufficiently to the bearings before the next shift operation. After the daily production, raw materials in the ring die holes must be squeezed out by the oil raw material, which would prevent the holes from blocking when operate in the following days. Routine weekly or biweekly maintenance procedures range from changing gearbox oil, changing roller shells, and drilling ring die holes etc. Ring die replacement and other repairs can be conducted during the monthly shutdown maintenance. The time of the maintenance differs from the scale of the production line.
Anyhow, the longer a facility accumulates a history of operations with accurate, dependable tracking of hours, the more it can rely on predictive versus preventative maintenance. The veteran maintenance usually have a detailed maintaining schedule, so that they know clearly about the daily and weekly predictive maintenance and annually preventative maintenance.
Consider it ironic, but plants have to go down to be effective when they’re up. The most important qualifier to this is being in control of when the plant is down—avoiding having to shut down versus planning a shutdown. Despite the limit of the equipment, what you can do to improve the throughput is to conduct correct and regular maintenance, and accumulate rich operation experience.