Research on RDF Pelletizing Technology
Municipal solid waste (MSW) is a very heterogeneous waste product and its composition and properties vary by source location and season. The primary organic components are plastics, paper, textiles, and food/wood waste, combined with inorganic metals, glass, and various composites.
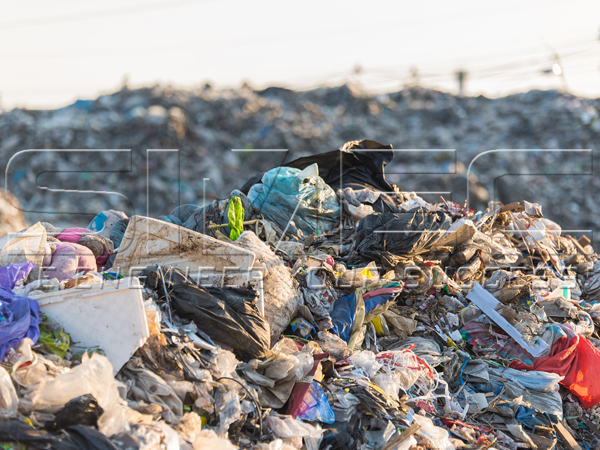
Municipal Solid Waste
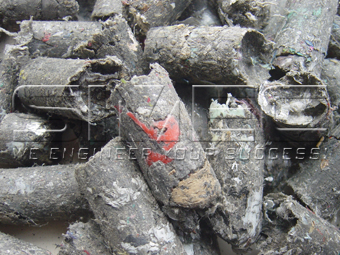
RDF Pellets
Combustible composition of MSW is a suitable feedstock for thermal conversion. Current technologies process the MSW into refuse-derived fuel (RDF) fluff before thermal conversion. It’s proved that the dense pellet is a better form to converse the RDF into biofuel considering the storage and transportation, cause it is more durable, easier to handle, and more uniform.
Pellets made of RDF have an average moisture content <10%, durability 88~94%, ash content 10~22%, and calorific value about 4000 kcal/kg. RDF Pellets can be used as solid fuel to replace coal in cement processing plants, steel mills, thermal power plants, agricultural and horticultural fields, etc.
SIMEC focus on technology R&D to make high quality RDF pellets.
For the RDF material, it’s found that moisture content, pressure, and grind size have significant influences on the density of the formed pellets. Moreover, by adjusting the process conditions such as applied pressure, die geometry & temperature, and pelletizaiton hold-time, the quality of RDF pellets can also be altered.
Pellets made of RDF have an average moisture content <10%, durability 88~94%, ash content 10~22%, and calorific value about 4000 kcal/kg. RDF Pellets can be used as solid fuel to replace coal in cement processing plants, steel mills, thermal power plants, agricultural and horticultural fields, etc.
SIMEC focus on technology R&D to make high quality RDF pellets.
For the RDF material, it’s found that moisture content, pressure, and grind size have significant influences on the density of the formed pellets. Moreover, by adjusting the process conditions such as applied pressure, die geometry & temperature, and pelletizaiton hold-time, the quality of RDF pellets can also be altered.
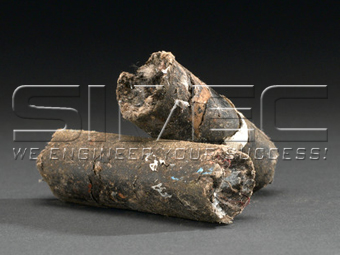
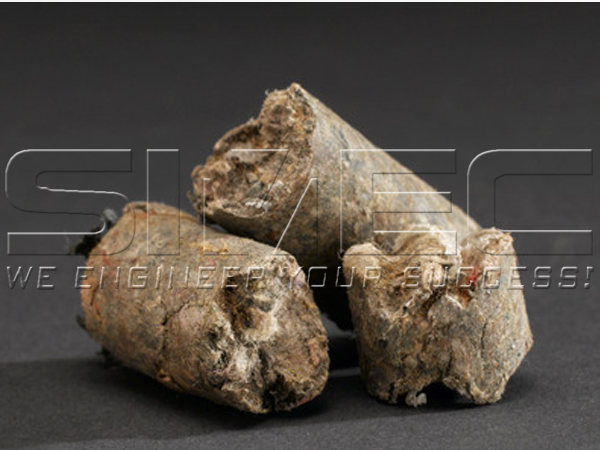
Controlling the raw material grind size, moisture content, and pressure of the pellet die in a reasonable range have positive correlations on improving density, tensile strength, as well as dimensional stability.
16% is proved to be a suitable initial moisture content for RDF pellet production. Pelleting resultes in a 1~10% decrease in moisture content depending on the initial moisture content and pelleting temperature. Pellet storage results in a further 1~3% decrease in moisture content of the pellets.
A larger pressing pressure contributes to higher compact pellet density. But there is less differentiation of the effect of pelleting pressure on tensile strength.
Though smaller RDF fluff results in higher pellet compact density and tensile strength, the grind size must be controlled in a reasonable range. Size reduction process needs to be economical and commercially viable. In SIMEC commercial RDF pellet projects, it is proved that RDF pellets with the diameter of 18~25mm produced from 25.4 mm or 50.8 mm grinded RDF are more uniform and easier to handle.
SIMEC SPM800 pellet mill is specially designed for RDF pelletization. The final RDF pellets have characteristics of High Compact Density, Good Dimensional Stability, Maximum Mass Yield, Lower Moisture Content, High Tensile Strength.
Till date there are more than 60 sets of SPM800 RDF pellet mills in service for Municipal Solid Waste treatment plants that create the best solution for solid fuel recovery from MSW. Average hourly production capacity is 2~2.5 tons/set.
16% is proved to be a suitable initial moisture content for RDF pellet production. Pelleting resultes in a 1~10% decrease in moisture content depending on the initial moisture content and pelleting temperature. Pellet storage results in a further 1~3% decrease in moisture content of the pellets.
A larger pressing pressure contributes to higher compact pellet density. But there is less differentiation of the effect of pelleting pressure on tensile strength.
Though smaller RDF fluff results in higher pellet compact density and tensile strength, the grind size must be controlled in a reasonable range. Size reduction process needs to be economical and commercially viable. In SIMEC commercial RDF pellet projects, it is proved that RDF pellets with the diameter of 18~25mm produced from 25.4 mm or 50.8 mm grinded RDF are more uniform and easier to handle.
SIMEC SPM800 pellet mill is specially designed for RDF pelletization. The final RDF pellets have characteristics of High Compact Density, Good Dimensional Stability, Maximum Mass Yield, Lower Moisture Content, High Tensile Strength.
Till date there are more than 60 sets of SPM800 RDF pellet mills in service for Municipal Solid Waste treatment plants that create the best solution for solid fuel recovery from MSW. Average hourly production capacity is 2~2.5 tons/set.
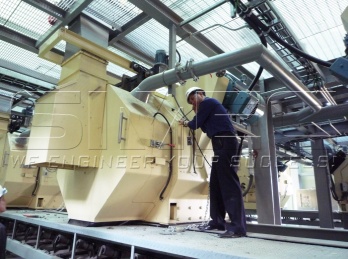
RDF Pellet Plant
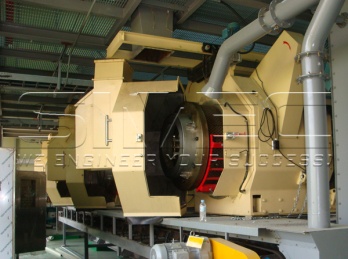
SPM800 RDF Pellet Machine
We believe SIMEC technology will contribute to more MSW RDF treatment projects globally.