Research on Bana Grass Carbonization
Bana grass is also known as the miracle grass, a hybrid variety with scientific name. Its name Bana is derived from the acronym ’ba’ in Babala and ‘na’ from Napier. Its amazing growth power makes it suitable for many purposes, from tall grass hedge to fuel and fodder.
Bana grass grows extremely rapidly in proper conditions. It also fares better than most other grasses even in a poor growing environment. The average yield per hectare per year of the bana grass is at 300 metric tons wet. Dried bana grass is also a prime energy crop from which power, heat and coal may be derived. For this kind of application, six months old harvesting is preferred to be able for the grass to develop its lignin content so the energy content is much higher.
That’s why SIMEC take bana grass as one of experimental feedstock to obtain more experiment data to help investors learn more about its application.
Date: Oct. 21, 2020
Raw Material: Bana Grass, moisture content 70%.
Step 1: Chopping and Natural Drying
Normally, height of bana grass can be up to 4~7 meters. For the convenience of transportation, the harvested bana grass has been chopped into 100~150mm length segment before delivered to us. And it’s naturally dried in the air in SIMEC R&D facility to adjust its moisture within right scope of charring.
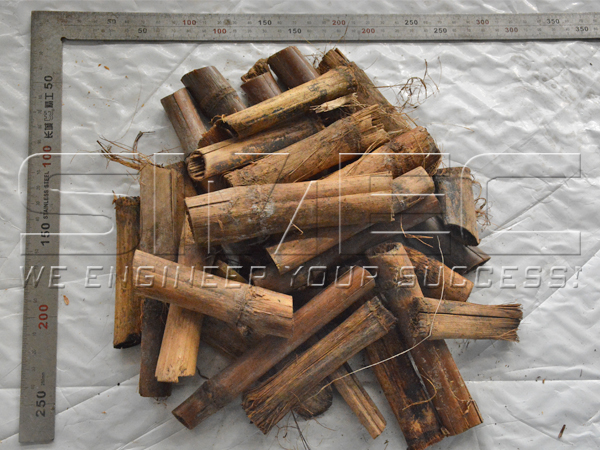
Violet Bana Grass
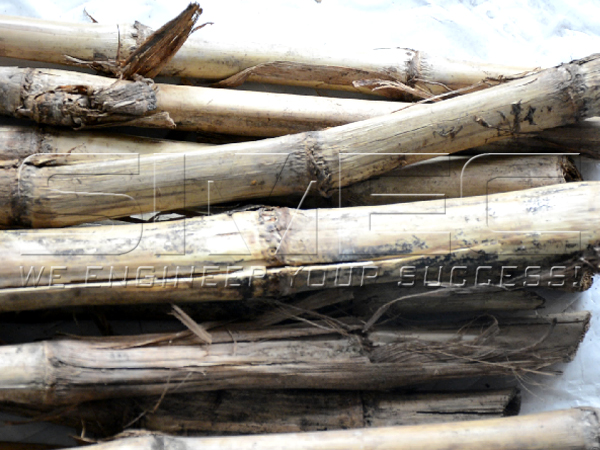
Bana Grass
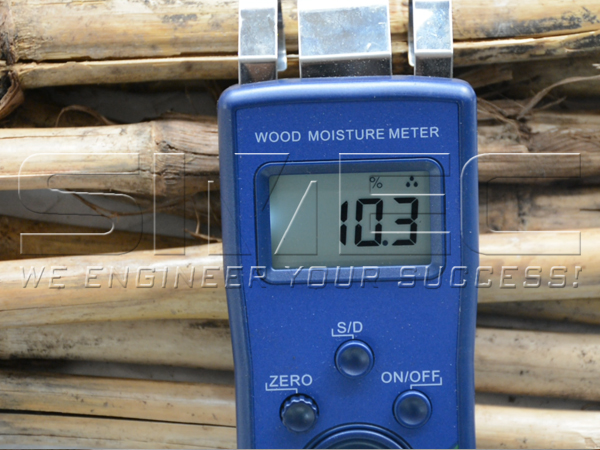
Bana Grass Moisture Content
Status: Chopped bana grass
Moisture: 10.6% after being dried.
Size: 100~150mm
Step 2: Shredding
Further more, we pretreat the chopped bana grass by size reduction processes which includes shredding and pulverizing. The further size reduction process requires utilization of SIMEC laboratory scale Shredder and Hammer Mill. The two kinds of equipment have complementary advantages, which can realize pulverizing of large size fibrous materials such as cornstalk, paddy straw, elephant grass and so on.
The main function of the lab shredder is to cut bana grass into small segments.
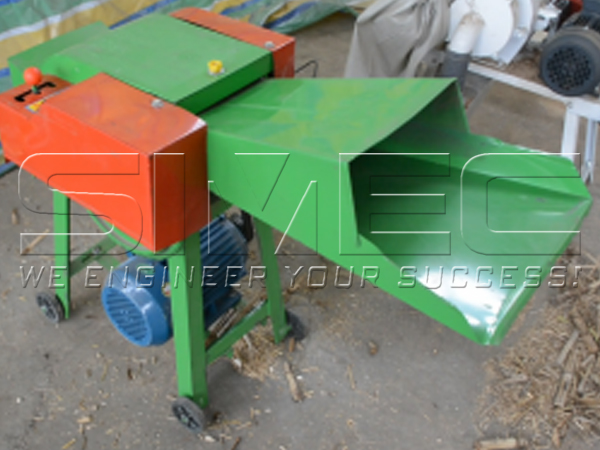
Bana Grass Shredder
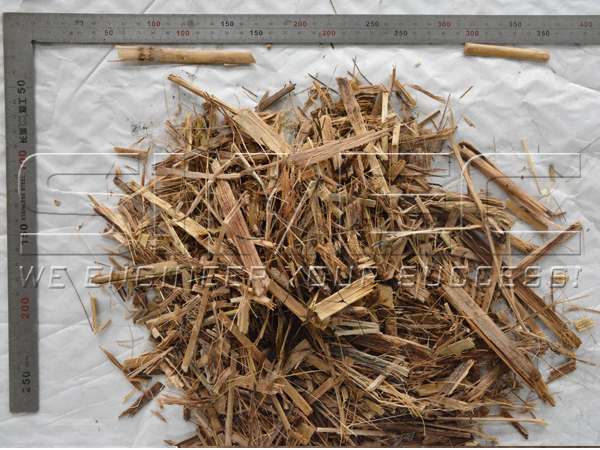
Shredded Bana Grass
Status: Shredded bana grass
Moisture: 9.5% after being shredded.
Size: 30~100mm
Step 3: Pulverizing
The shredded material can be further pulverized to the proper size by the lab scale hammer mill. By replacing the screen at the bottom of the hammer mill, the output size of material can be adjusted. In this experiment, the lab hammer mill equips with a 6mm sieve to process the raw material, and most of the final pulverized material is under 5mm, while a small part is in the range of 5-10mm. The output size can meet the requirements of feeding, discharging and charring reaction.
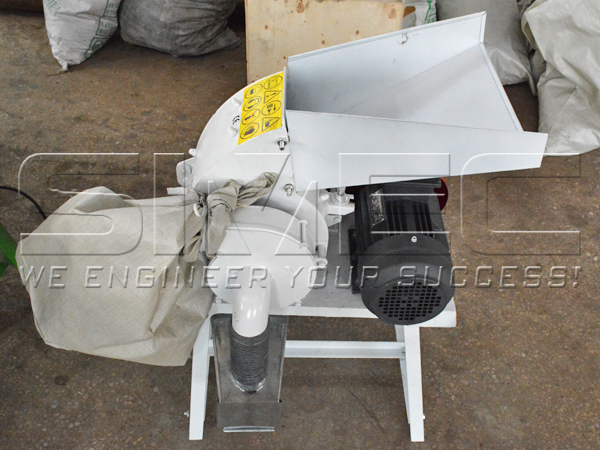
Bana Grass Hammer Mill
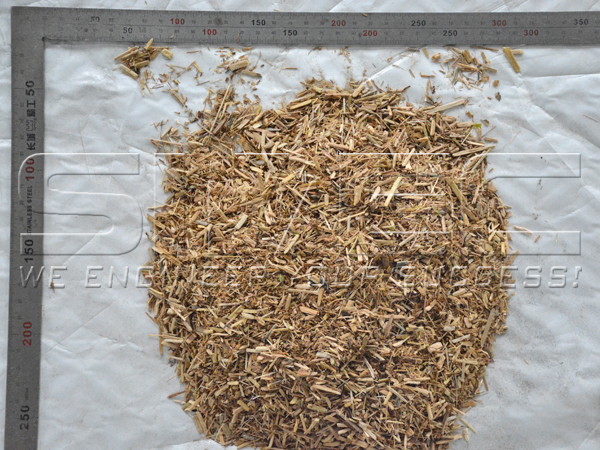
Pulverized Bana Grass Size
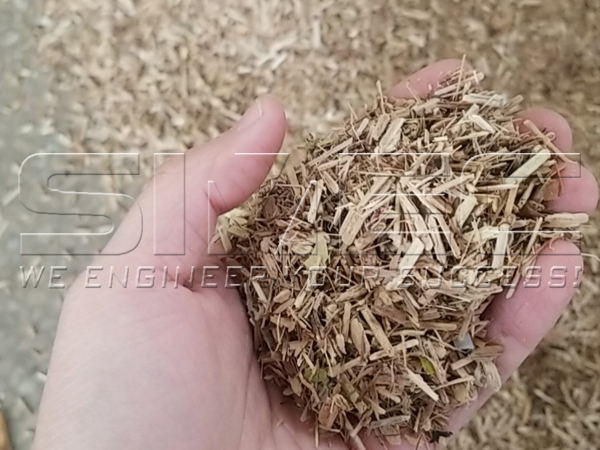
Pulverized Bana Grass
Moisture: 7.9%
Size: 5~10mm
Step 4: Charring
Charring test is carried out by Biomass Laboratory Pyrolysis Apparatus . The compact design of the equipment enables the operator to conduct biomass pyrolysis experiments in a limited space. The simple and accurate operation of this equipment help the clients, who will set up commercial biomass pyrolysis projects, to collect the relevant experimental data for further analysis and research, then improve commercial operation.
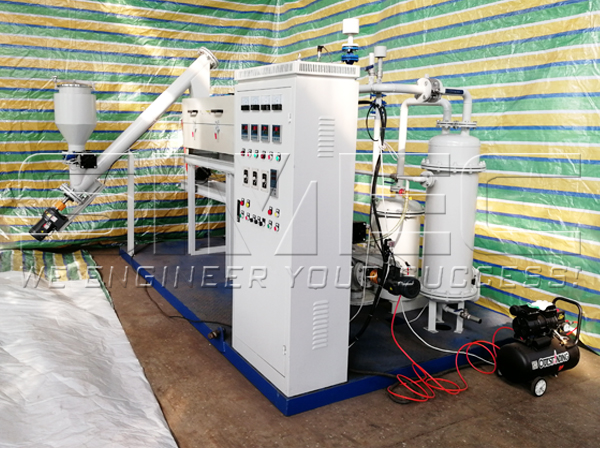
Biomass Laboratory Pyrolysis Apparatus
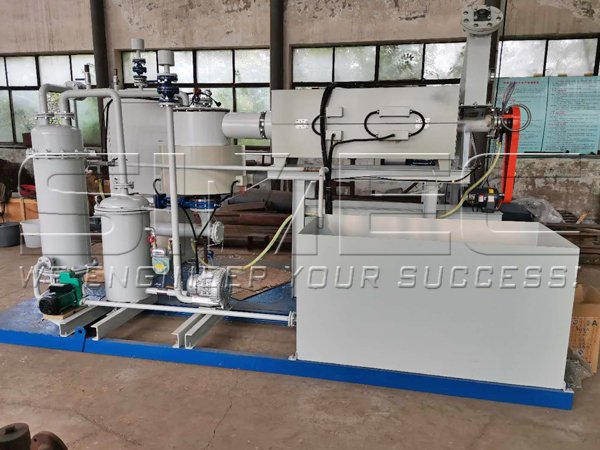
Rear View of Biomass Pyrolysis Apparatus
Features:
- The equipment is adopted with PID intelligent temperature controlling & monitoring system, which makes sure the highly precise and stable reacting temperature;
- The specialized control cabinet enables simple operation & adjustment;
- Accessible Gas Sampling: It is convenient to collect the syngas through the special designed syngas sampler at Sampling Interfaces.
- Including syngas burners, and flame temperature detector.
- Modular design contributes to minimizing clients’ installation and commissioning work. Before delivery, all of the mechanical and electrical components will be mounted on specially designed operation platform, and commissioned in SIMEC fabrication mill. The completely mounted apparatus can be loaded into a standard 20’ shipping container.
- Optional Syngas Online Monitoring and Analysis Module enables the researcher to gain complete data of synthetic gas, such as composition, proportion, thermal value, etc., and to graph dynamic data curves. Detectable gas range: CO, CH4, H2, CO2, N2, C2H6, C3H8, CnHm, etc. The detectable gas range can be customized according to client’s requirements.
We set reaction temperature at 600℃. It takes 30 minutes to rise the temperature from 150℃ to 600℃.
Then, we feed pulverized bana grass into the feeding hopper and cover the top cap to isolate the air. Then, open the sluice valve to feed the materail into pyrolysis reaction chamber.
The feeder adopts variable frequency speed design. A stable material feeding flow which is required by charring process can be achieved by setting the feeding speed at 27Hz.
The pyrolysis reactor can also adjust the residence time as per requirement. To char bana grass, it is set at 15~17Hz to realize continuous and stable reaction.
After loading the material, it took 14 minutes before syngas generating.
After being purified by a complete set of purification devices, the generated combustible syn-gas is ignited at the No. 2 burner. The temperature of the flame reaches 680℃. No harmful gases were discharged into the air during the whole experiment.
The syngas is quite pure, easy to be ignited. The combustion performance is good. From the test, it indicates that the syngas is sufficient for power generation.
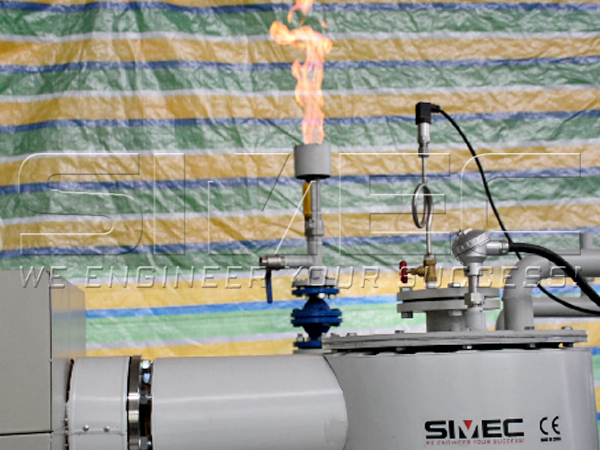
Purified Syngas Combustion
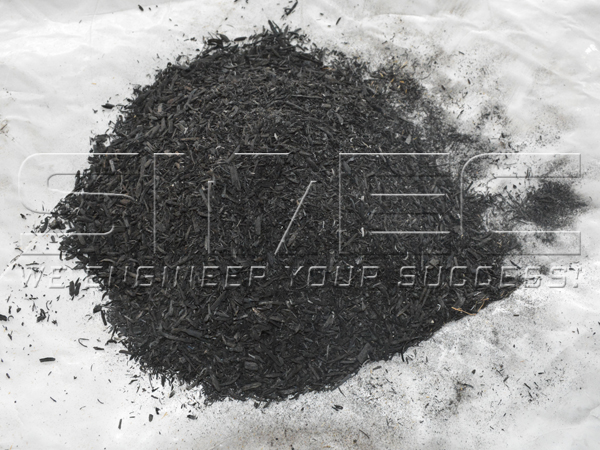
Bana Grass Charcoal
Status: Bana Grass Charcoal
Process Temperature: 600℃
Carbon Tank Temperature: 50℃
Processing Speed: 15~17Hz
Weight Before Carbonization: 9.15 kg
Weigh After Carbonization: 2.3 kg
The char sample needs to be tested to obtain its detail specification. The following parameters will be tested accordingly:
Total Carbon Content
Fixed Carbon Content
Heating Value
Moisture Content
Ash Content
Volatile Matter Content
CONCLUSION
A continuous and stable charring reaction of bana grass can be achieved at a 600 ℃ process temperature. Uniform size and moisture of bana grass is helpful to keep continuous and stable charring process. The charcoal production ratio is about 25% at 600℃. The process can produce sufficient amount of combustible gases. The gases can be used to sustain carbonization, or to generate power.
In conclusion, the bana grass is a high quality energy grass for char production. Its large-scale co-generation of char and gas will have good economic and environmental benefits.
© Copyright of articles and pictures on this site belongs to SIMEC. Any company, media, website or individual are not allowed to reprint, reproduce, repost, modify or use in other ways without permission. Otherwise SIMEC will have the right to pursue legal responsibilities.