How to Adjust the Clearance Between Rollers and Ring Die
Generally clearance should be 0.05-0.3mm. Clearance between new die and rollers can be measured with feeler gauge. If adjusting the clearance during ordinary production, control clearance to the following manner: when turning die with hands, rollers rotate intermittently and just touch the die through visual inspection.
For new die, clearance should be smaller. After clearance adjustment, tighten the related nuts and screws and replace the feed cone in the reverse sequence to that previously described. Make sure that the retaining nuts and lock screws have been tightened to avoid looseness and damage to the machine during operation.
Pelletizing Chamber of SPM780 Pellet Mill
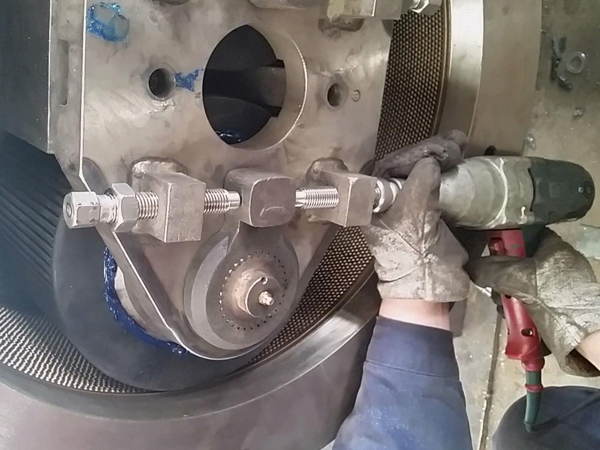
Open the pellet chamber door, loosen the fastening bolts of the feed cone (See Figure 1), hold two handles of feed cone tightly with hands, turn the feed cone clockwise, thus feed cone can be removed. Then clear away the accumulated material on the inside surface of die (1) and surface of rollers (3), loosen lock screws (2) and retaining nuts (6) twist the adjusting screw (7) so as to make the roller adjusting quadrant (10) turn. Clearance becomes smaller when making adjustment in the arrow direction of the roller adjusting gear, and clearance becomes bigger when making adjustment in the opposite direction. If adjustment cannot be made in the shown direction, it means rollers are mounted wrong and must be mounted again. It is vital rolls are adjusted counter-clockwise to close the gap.
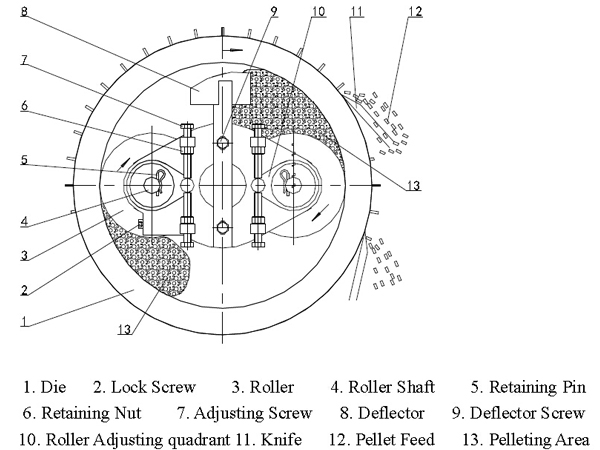
SIMEC would react on your post-sale support request within 24 hours. Prompt and contributing solutions could be provided by our domestic professional engineering team remotely or on site.