Critical Parameters of Biomass Torrefaction Process
Power producing plants are major emitters of greenhouse gases. A large amount of the flue gases from combustion of fossil fuels mainly composed of CO2, NOx, SOx and water vapor are released into the atmosphere. These gases are hazardous to the environment.
It’s very important to reduce the amount of hazardous gases, and reduce their dependence on coal reserves. To achieve the target, biomass, that has undergone torrefaction, can be used to replace a certain amount of coal. Torrefied biomass can be utilized in existing large scale combined heat and power (CHP) plants to co-fire with coal without having to change the design. Biomass is considered to be one of the most important renewable fuels, since the gases emitted from torrefied biomass combustion are part of the carbon cycle as biomass is produced from CO2 absorbed from the atmosphere during photosynthesis.
The critical parameters of biomass torrefaction process include temperature, oxygen content, heating rate and residence time. Based on project practice of SIMEC, it is observed that a temperature range between 275 and 300 ℃ under inert conditions with a heating rate of 10 ℃/min and residence time between 20 and 40 min are required to achieve the best biomass with properties comparable to those of coal. This made it possible to co-fire the biomass with coal for energy production at different proportions. When torrefied biomass is co-fired with coal and the net CO2, NOx and SOx emissions will be reduced thereby reducing environmental damage.
Torrefaction occurs when thermal heat is carefully applied to biomass under controlled thermodynamic conditions causing chemical, physical and mechanical changes to the biomass. Energy density of biomass can be enhanced by thermal treatment and pelletization processes.
It’s very important to reduce the amount of hazardous gases, and reduce their dependence on coal reserves. To achieve the target, biomass, that has undergone torrefaction, can be used to replace a certain amount of coal. Torrefied biomass can be utilized in existing large scale combined heat and power (CHP) plants to co-fire with coal without having to change the design. Biomass is considered to be one of the most important renewable fuels, since the gases emitted from torrefied biomass combustion are part of the carbon cycle as biomass is produced from CO2 absorbed from the atmosphere during photosynthesis.
The critical parameters of biomass torrefaction process include temperature, oxygen content, heating rate and residence time. Based on project practice of SIMEC, it is observed that a temperature range between 275 and 300 ℃ under inert conditions with a heating rate of 10 ℃/min and residence time between 20 and 40 min are required to achieve the best biomass with properties comparable to those of coal. This made it possible to co-fire the biomass with coal for energy production at different proportions. When torrefied biomass is co-fired with coal and the net CO2, NOx and SOx emissions will be reduced thereby reducing environmental damage.
Torrefaction occurs when thermal heat is carefully applied to biomass under controlled thermodynamic conditions causing chemical, physical and mechanical changes to the biomass. Energy density of biomass can be enhanced by thermal treatment and pelletization processes.
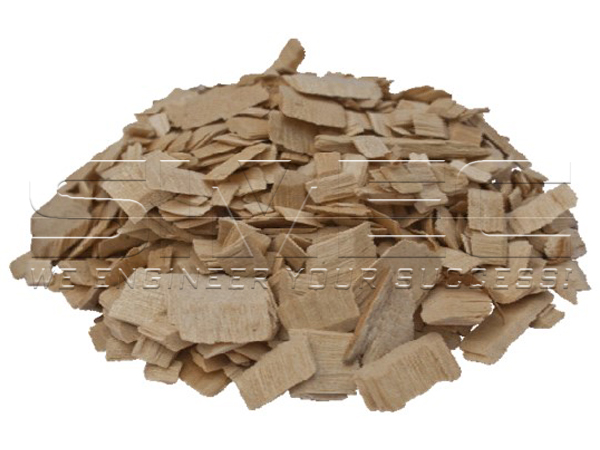
Raw Biomass
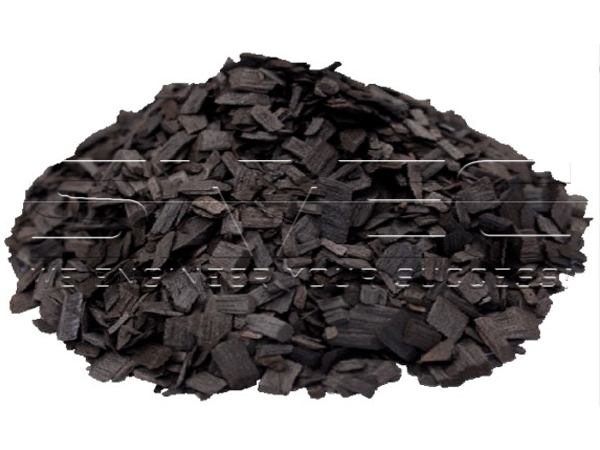
Torrefied Biomass
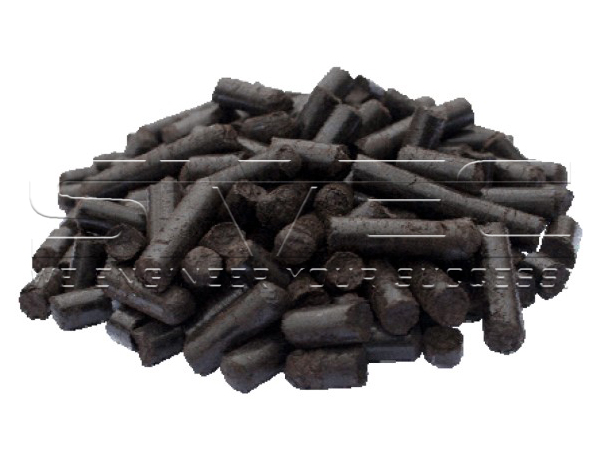
Torrefied Biomass Pellets
The temperature range of torrefaction is between 200 and 300 ℃ and the process should occur under inert conditions, at low heating rates and low residence time. Slow heating rate allows maximization of solid yield of the torrefaction process. Usually, biomass with higher hemicellulose content will result in lower yield while biomass with lower hemicellulose gives higher yield. Torrefaction yield can vary between 24% and 95% of the original raw biomass weight. Weight loss will increase when torrefaction temperature increases due to moisture removal and hemicellulose breakdown which can produce H2O, CO, CO2, and other hydrocarbons.
Biomass is mostly composed of cellulose, hemicellulose and lignin. The major degradation of hemicellulose starts from around 200 ℃. Lignin starts degrading from around 275 ℃, whilst cellulose starts degrading from 330 ℃.
During torrefaction, hemicellulose is mostly decomposed as it is active within the range 200 - 300 ℃.
The volatiles released during this process can be burned in a combustor, and the flue gases collected and used to preheat raw biomass. Advanced technologies can maximize the energy efficiency of biomass. In a SIMEC biomass torrefaction line, the torrefying process is self-sustained. External heat input is unnecessary.
SIMEC torrefaction reactor operated continuously and an inert gas (N2) was used to purge O2 from the reactor during preheating, torrefaction process, and also when cooling down from torrefaction temperature to room temperature to avoid biomass ignition and causing a fire hazard. SIMEC R&D efforts focus on finding the optimized torrefaction parameters by minimizing biomass weight loss and maximizing biomass higher heating value. However, the optimal parameters vary when torrefying different biomasses.
Biomass is mostly composed of cellulose, hemicellulose and lignin. The major degradation of hemicellulose starts from around 200 ℃. Lignin starts degrading from around 275 ℃, whilst cellulose starts degrading from 330 ℃.
During torrefaction, hemicellulose is mostly decomposed as it is active within the range 200 - 300 ℃.
The volatiles released during this process can be burned in a combustor, and the flue gases collected and used to preheat raw biomass. Advanced technologies can maximize the energy efficiency of biomass. In a SIMEC biomass torrefaction line, the torrefying process is self-sustained. External heat input is unnecessary.
SIMEC torrefaction reactor operated continuously and an inert gas (N2) was used to purge O2 from the reactor during preheating, torrefaction process, and also when cooling down from torrefaction temperature to room temperature to avoid biomass ignition and causing a fire hazard. SIMEC R&D efforts focus on finding the optimized torrefaction parameters by minimizing biomass weight loss and maximizing biomass higher heating value. However, the optimal parameters vary when torrefying different biomasses.
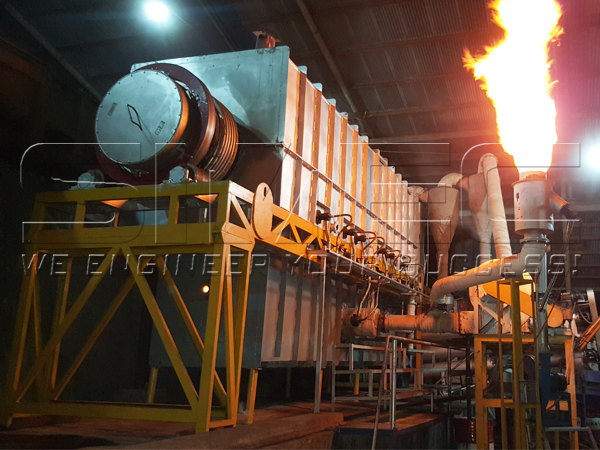
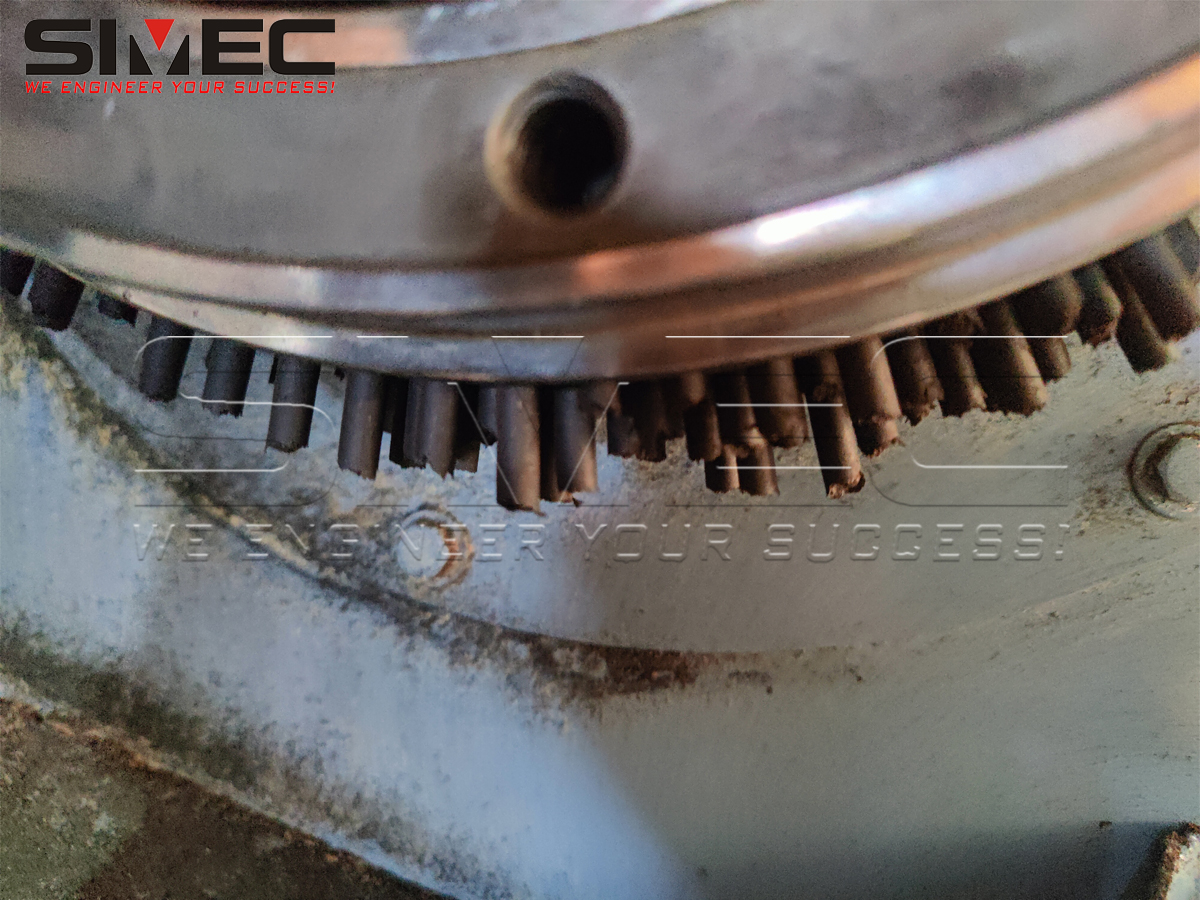
Weight loss at 200℃ and below is attributed to loss of remaining bound and unbound moisture. But weight loss at 200 - 300 ℃ is mainly due to devolatization of organics when the hemicellulose starts to breakdown by bond breakage.
As hemicellulose breaks down, H2O is produced from its –C–O–H bonds, leading also to production
of non-condensable gases like CO and CO2. Of these three, H2O is the most abundant at 250 ℃. Since the volatiles have low energy value. The energy loss of torrefied biomass is much lower than mass loss. Thus the energy density is enhanced.
For most of the biomasses, there are three important phases involved in the torrefaction process.
As hemicellulose breaks down, H2O is produced from its –C–O–H bonds, leading also to production
of non-condensable gases like CO and CO2. Of these three, H2O is the most abundant at 250 ℃. Since the volatiles have low energy value. The energy loss of torrefied biomass is much lower than mass loss. Thus the energy density is enhanced.
For most of the biomasses, there are three important phases involved in the torrefaction process.
- The first phase mainly consists of free and bound water extraction from biomass at 100-200 ℃.
- The second phase is irreversible biomass degradation that occurs from 200 to 250 ℃.
- The third phase, which occurs between about 250 and 330 ℃, usually involves the total destruction of most reactive component of lignocellulose, hemicelluloses.
The destruction of cellulose occurs between about 330 and 370 ℃ which goes beyond the scope of torrefaction.
With an increase in temperature, the torrefied biomass turns darker from the raw brown color, to dark brown at 200 ℃, blackish brown at 250 ℃ and black at 300 ℃. The change in color is because of increased hemicellulose breakdown leaving higher content of carbon black.
With an increase in temperature, the torrefied biomass turns darker from the raw brown color, to dark brown at 200 ℃, blackish brown at 250 ℃ and black at 300 ℃. The change in color is because of increased hemicellulose breakdown leaving higher content of carbon black.
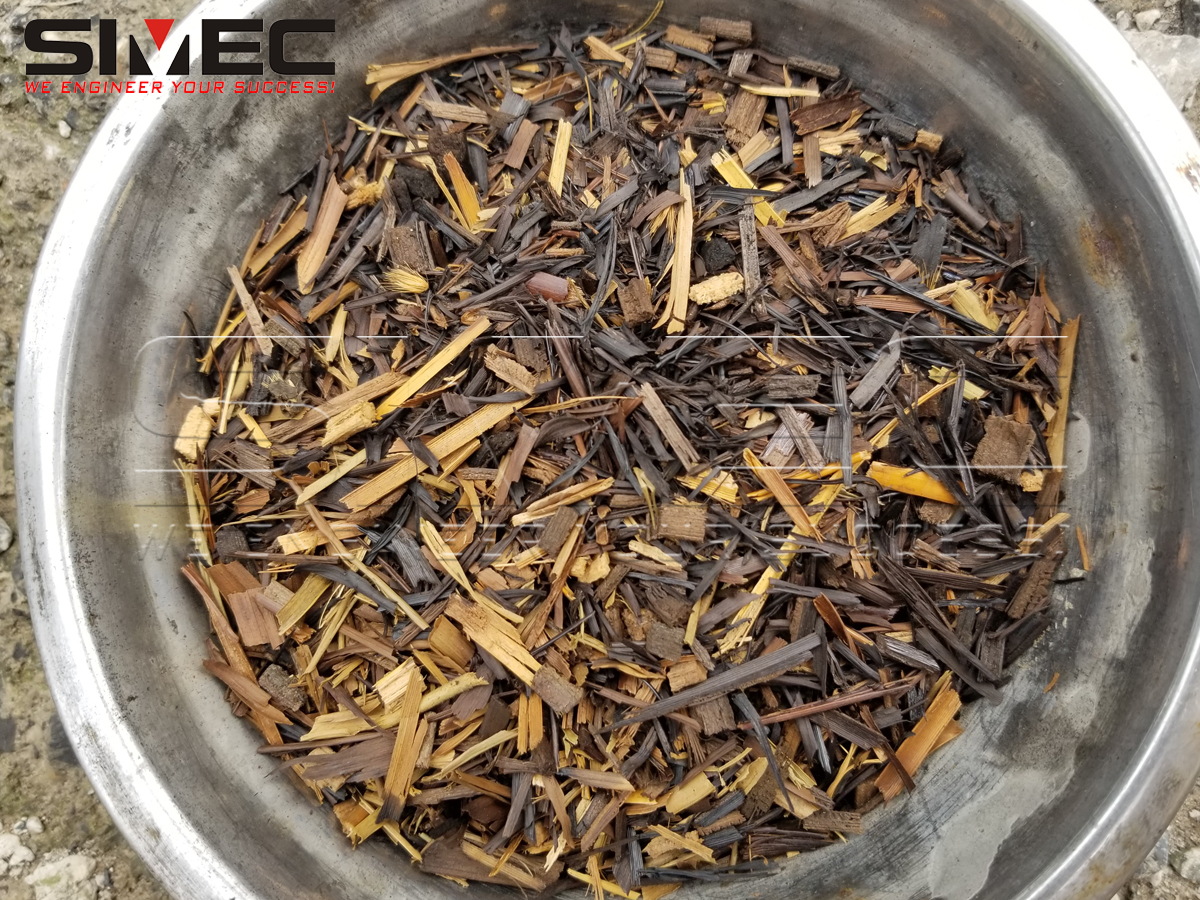
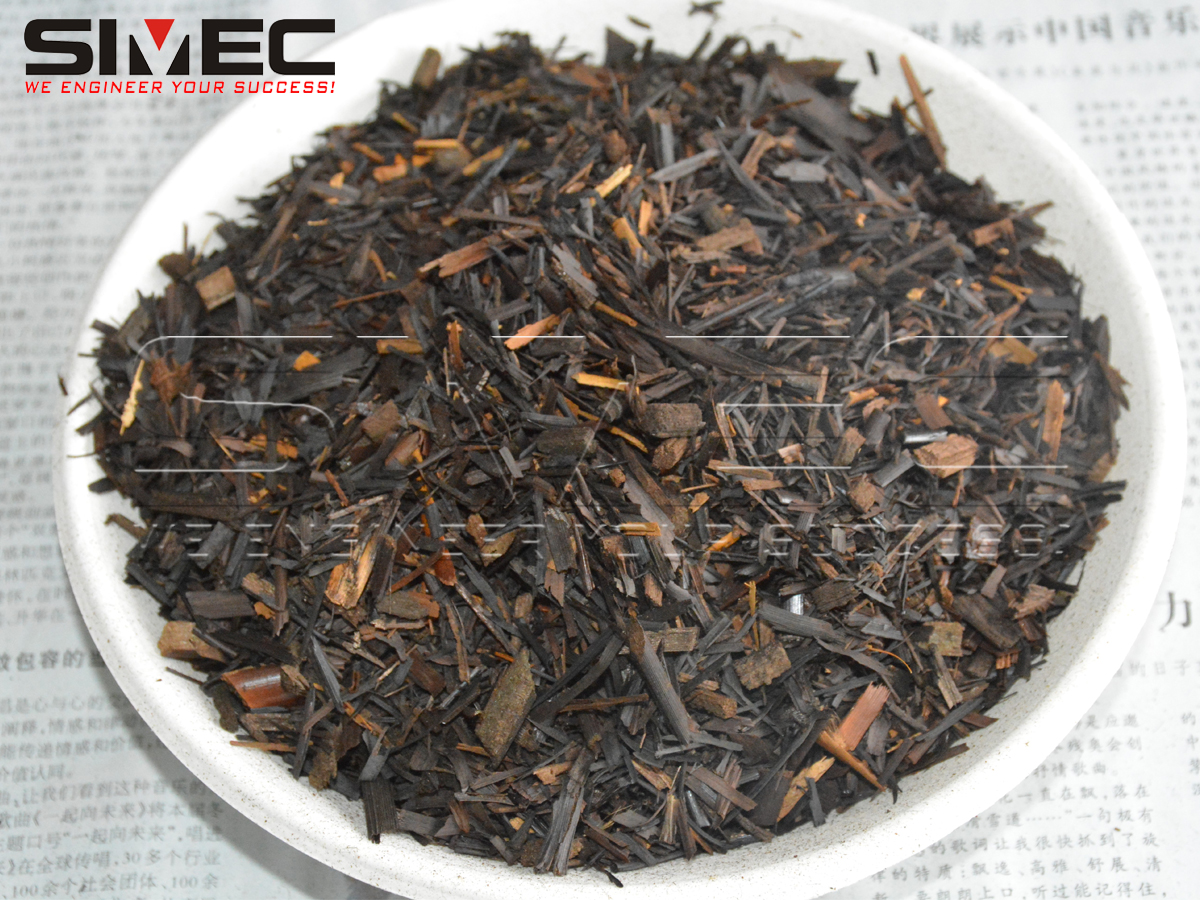
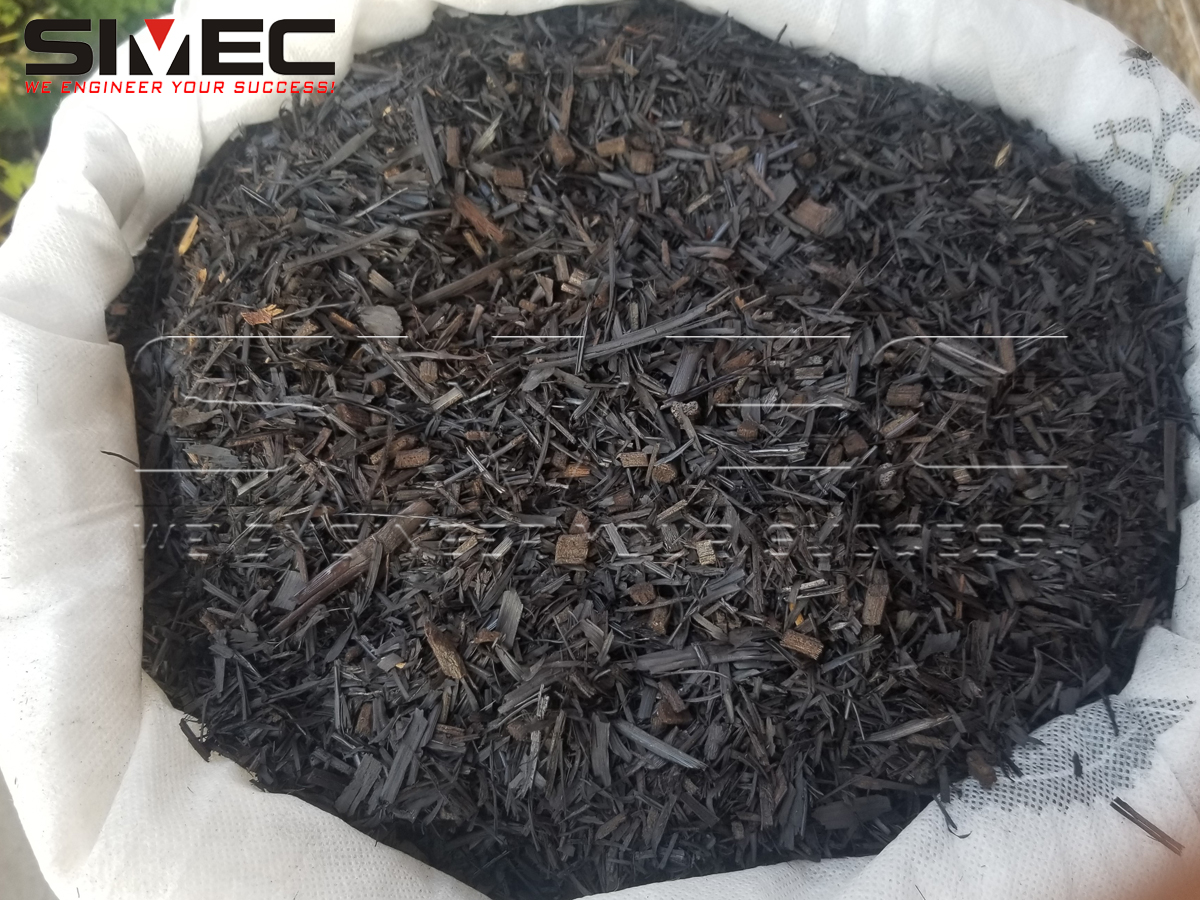
Slower heating rate is good for torrefaction as it can result in higher solid yields. Optimum heating rate was observed to be 10 ℃/min which resulted in biomass with higher mass yield, HHV, energy yield and energy density. Higher heating rates promote dehydration and decarboxylation reactions which results in volatiles being removed rapidly in a short period of time thereby densifying the biomass energy.
Short residence time helps to reduce weight loss, attributed to limited devolatilisation of hemicellulose of the biomass. But energy density of torrefied biomass increases with an increase in residence time. For most of the biomasses, the optimal residence time can be regulated between 20 and 40 minutes.
As a final summary, we can make a conclusion that non-oxidative conditions with low heating rates and shorter residence time resulted in the best torrefied biomass.
© Copyright of articles and pictures on this site belongs to SIMEC. Any company, media, website or individual are not allowed to reprint, reproduce, repost, modify or use in other ways without permission. Otherwise SIMEC will have the right to pursue legal responsibilities.
Short residence time helps to reduce weight loss, attributed to limited devolatilisation of hemicellulose of the biomass. But energy density of torrefied biomass increases with an increase in residence time. For most of the biomasses, the optimal residence time can be regulated between 20 and 40 minutes.
As a final summary, we can make a conclusion that non-oxidative conditions with low heating rates and shorter residence time resulted in the best torrefied biomass.
© Copyright of articles and pictures on this site belongs to SIMEC. Any company, media, website or individual are not allowed to reprint, reproduce, repost, modify or use in other ways without permission. Otherwise SIMEC will have the right to pursue legal responsibilities.