Briquetting Optimizes Paddy Straw Torrefaction
Paddy straw, a prevalent agricultural waste, is widespread in Asian countries. These nations produce approximately 667 million tonnes of paddy straw annually, with India alone contributing about 140 million tonnes. Traditionally, farmers dispose of paddy straw by burning it on their farmlands post-harvest. However, this practice leads to numerous issues, including air pollution, decreased soil fertility, and an increase in respiratory diseases.
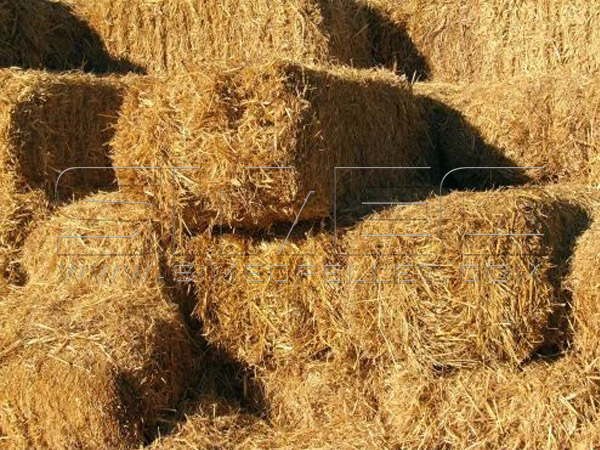
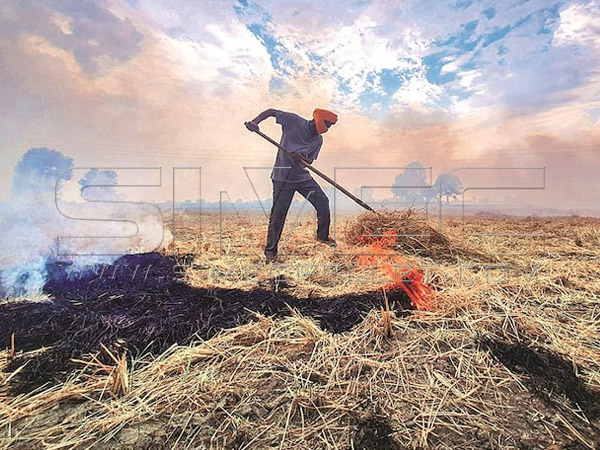
Converting paddy straw into renewable energy has gained popularity in India. Compared to fossil fuels, biomass renewable fuel generates fewer acid emissions and can achieve carbon-neutral combustion. After undergoing a series of pretreatments, paddy straw is processed into briquettes or pellets, which is beneficial for handling and transportation. The briquettes and pellets are acceptable fuels for biomass boilers, but cannot be co-fired in high proportions with pulverized coal in power plants.
To address these challenges and make paddy straw suitable for energy applications, some form of pretreatment is necessary to alter its physical and chemical properties. In recent years, biomass torrefaction technology has garnered significant attention. As a mild thermal chemical reaction, torrefaction converts biomass into a coal-like renewable fuel known as biocoal. Biocoal can substitute fossil fuels in various applications, such as cook stoves, industrial boilers and furnaces, thereby minimizing pollution. In thermal plants, it can be co-fired directly with coal without requiring boiler modifications.
Torrefaction is a mild pyrolysis process that typically occurs in an anaerobic environment, with the reaction temperature strictly controlled between 230°C and 300°C. This process alters the physical and chemical composition of paddy straw. Physical changes include a reduction in biomass volume, increased brittleness, and easier grinding. Chemical changes consist of increased hydrophobicity, carbon content and calorific value, a decrease of volatile matter. Consequently, torrefied biomass exhibits higher energy density, outstanding hydrophobicity, higher calorific value, and excellent grindability.
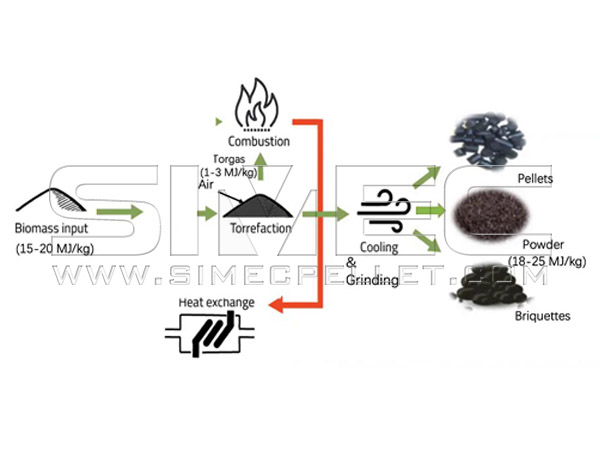
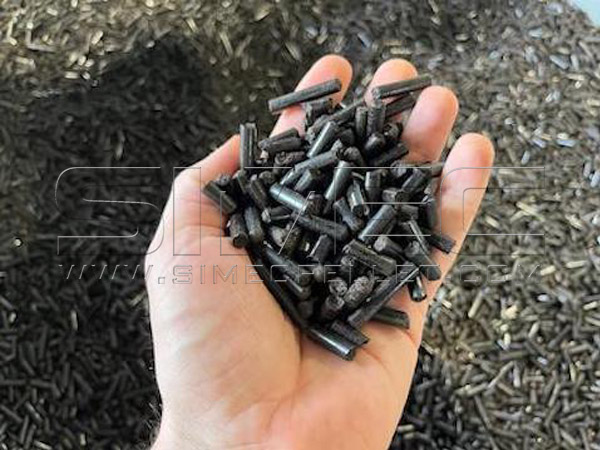
In practical applications, torrefied paddy straw is usually compressed into dense torrefied pellets, making the biomass more conducive to transportation and storage. Before thermal decomposition in a torrefaction reactor, the paddy straw will firstly go through a drying stage. Then the bulk density of shredded paddy straw at 10% moisture content can be as low as 70 kgs/m3. This will significantly reduce processing capacity of torrefaction reactor. Therefore, it is essential to convert paddy straw into briquettes prior to torrefaction. Bulk density of paddy straw briquettes can be increased to 350-400 kgs/m3. So the mass input and mass output of torrefaction reactor will be 4-5 times more. Heat penetration process during torrefaction can also be optimized.
Biomass briquette machine can convert shredded paddy straw into solid briquettes with higher bulk density and ease of handling. SIMEC technology can process raw materials with up to 25% moisture. The conventional size of biomass briquetting: cross-section 32×32mm, length 30-100mm, cross-sectional size is fixed, and the length can be appropriately adjusted according to needs.

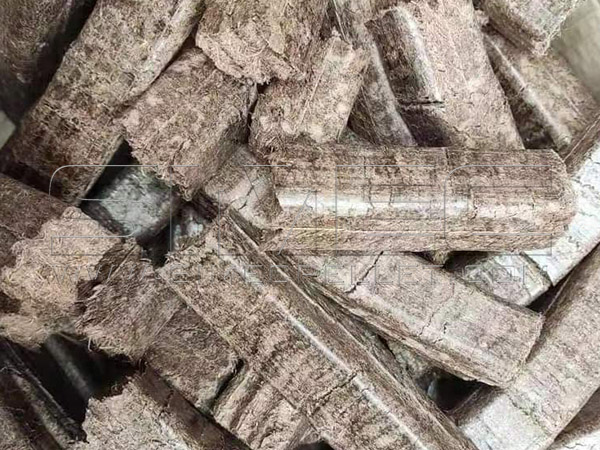
SIMEC offer tailored, cutting-edge biomass torrefaction technology, suitable for large-scale production. The patented AF-SFB torrefaction reactor features innovative energy recycling mechanism that ensures heat penetration into the biomass, enhancing energy savings and torrefaction efficiency. Fully automatic control guarantees stable quality of torrefied biomass.
© Copyright of articles and pictures on this site belongs to SIMEC. Any company, media, website or individual are not allowed to reprint, reproduce, repost, modify or use in other ways without permission. Otherwise SIMEC will have the right to pursue legal responsibilities.