Torrefaction of Napier Grass at 330°C
Torrefaction of napier grass can convert it to be coal-like product that features higher calorie density, hydrophobic, grindability. The physical appearance and the energy content of torrefied napier grass are similar to coal and even surpass in some instances. For example, the specific energy consumption of grinding torrefied napier grass is several times less than that of fossil coal. Thus, torrefied napier grass presents significant advantages when it’s utilized in existing combined heat and power (CHP) plants to co-fire with coal without having to change the design of CHP plants.
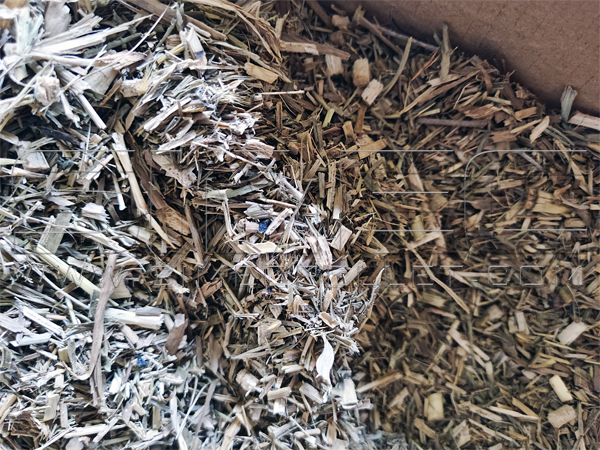
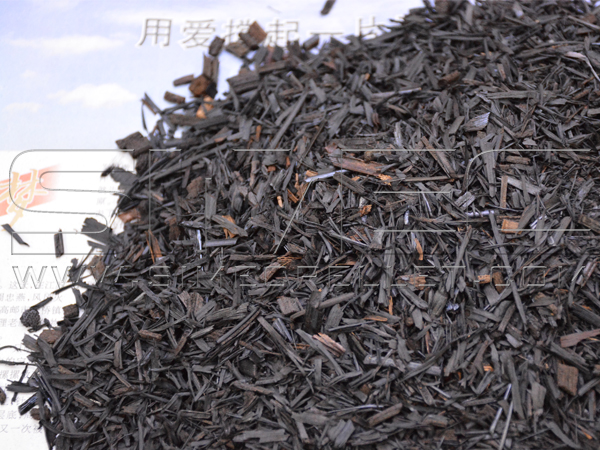
Napier grass has high cellulose content that can be used as a carbon (energy) source. Cellulose make up the largest proportion of napier grass about 50% by weight, followed by hemicelluloses which is about 30%, and lignin about 20%. To verify the performance of napier grass torrefaction at higher temperature but minimize the degrading of cellulose, SIMEC researchers launched a research program at 11th May 2024. The torrefaction research program includes the following steps:
1. Leaching of shredded napier grass;
2. Dewatering & Drying process;
3. Torrefaction of napier grass at 275℃, 300 ℃ and 330 ℃.
4. Grinding of torrefied napier grass.
5. Pelletization treatment to make diameter 8mm bio-coal pellets.
6. Laboratory analysis of torrefied pellets.
After multi times of torrefaction tests adopting a series of reaction parameters, the optimal torrefaction parameters were found by minimizing biomass weight loss and maximizing high heating value. With an increase in temperature, it was observed that torrefied napier grass turned darker from raw brown color, to blackish brown at 275℃, black at 300℃ and dark black at 330 ℃. The change in color was because of increased hemicellulose breakdown leaving higher content of carbon black.
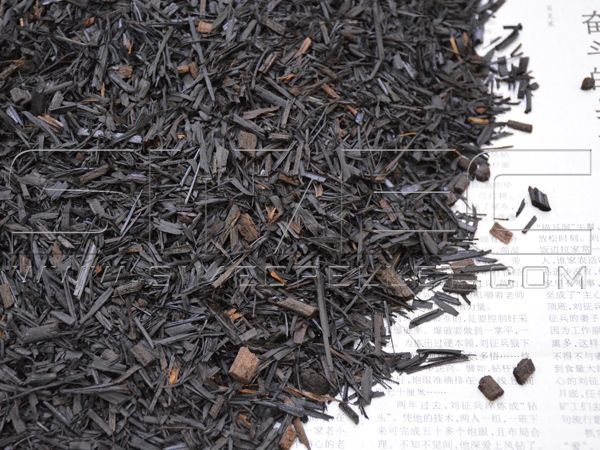

Please check the analysis result below issued on 19th May 2024. It can be seen that the calorific value of torrefied napier grass can reach up to 23.4 MJ/KG. Black pellets made of napier grass feature high mechanical durability and grindability, hydrophobic and low ash content.
Moisture Mt % |
Ash Content Ad % |
Volatile Matter Content Vad % |
Fixed Carbon Content Fcad % |
St,d% |
High Heating Value Qgrad Cal/g |
Low Heating Value Qnetv Cal/g |
3.12 | 8.61 | 46.72 | 44.67 | 0.047 | 5574 | 5227 |
According to SIMEC researchers’ tests and analysis results, torrefaction of napier grass at 330 ℃ resulted in very high heating value, but without causing difficulties in the pelletizing process. High energy density black pellets can be qualified substitute for coal in power generation plants.
© Copyright of articles and pictures on this site belongs to SIMEC. Any company, media, website or individual are not allowed to reprint, reproduce, repost, modify or use in other ways without permission. Otherwise SIMEC will have the right to pursue legal responsibilities.