Torrefaction Process Discription
Torrefaction is a kind of new way of dealing biomass pellet, it is a mild pyrolysis process that increase the value of biomass. This thermal pretreatment of biomass improves its energy density, reduces its oxygen-to-carbon (O/C) ratio, and reduces its hygroscopic nature.
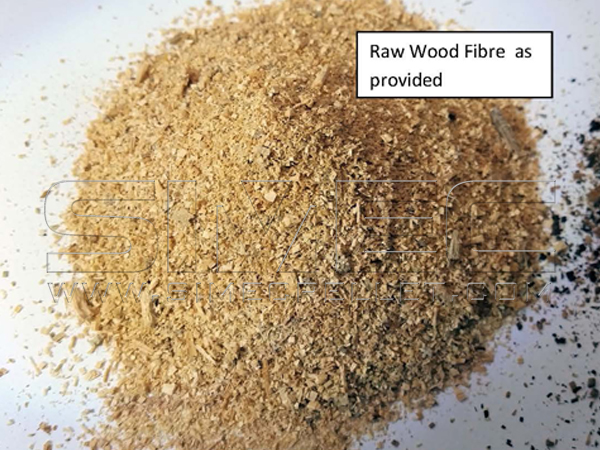
Raw Wood Fibre as Provided
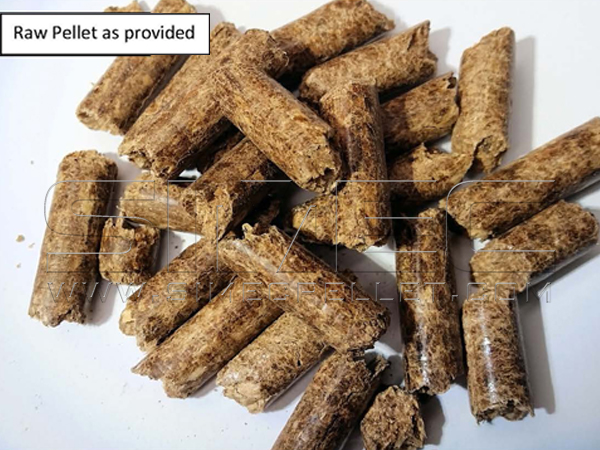
Raw Pellet as Provided
The prepared and sized material is fed from the hoppers to the Torrefaction system where the reactor process follows a closed loop control program that can vary the amount of gas to char production based on the energy requirement.
A basic summary of the Torrefaction system is described as:
The biomass material is fed into a preheat/drying chamber and transported through a low temperature zone, where the free water of the material can be dried off. Meanwhile, as the material temperature increasing in this chamber, the oxygen content of the ambient air will reduce.
Having passed through this stage, the material is then loaded into a lock hopper, where once the material is filled, the entry will be closed and the exit be opened. When the material is unloaded, the exit is closed, the entry opened and the loading cycle repeats. Once the material is inside the reactor chamber, the temperature and the internal pressure increase, and the ambient air is now at nearly zero oxygen. Any oxygen available is burned out with little effect to the large percentage of biomass in the reactor. As the material passes through the reactor, it is undergoing a change to its molecular state. When temperature is up to 100⁰C, any bound water is dried off and the particles dried out. At 200-400⁰C molecules of biomass decompose into solid and liquid yield along with non-condensable gases. This is called “Primary Torrefaction” and it occurs further down the reactor. Then the material travels further in the reactor, vapours are extracted and condensed as “tar” or “bio-oil”, while large molecules continue to be cracked yielding char at 300-500⁰C. This is called “Secondary Torrefaction”.
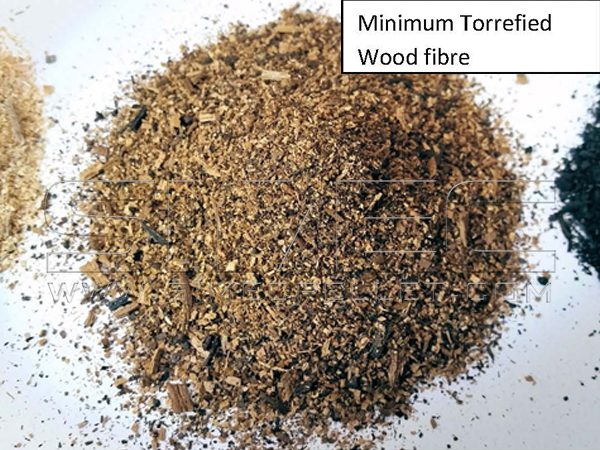
Minimum Torrefied Wood Fibre
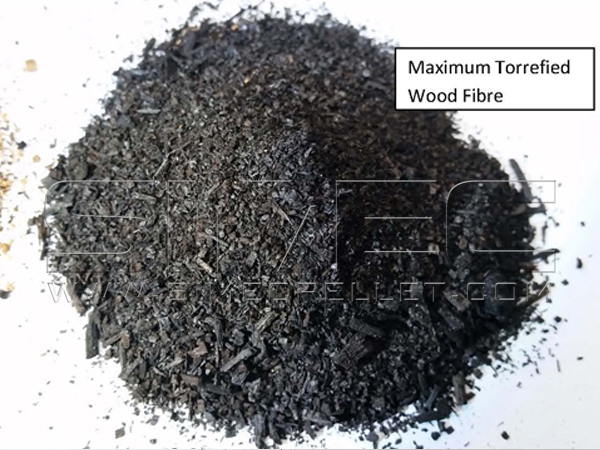
Maximum Torrefied Wood Fibre
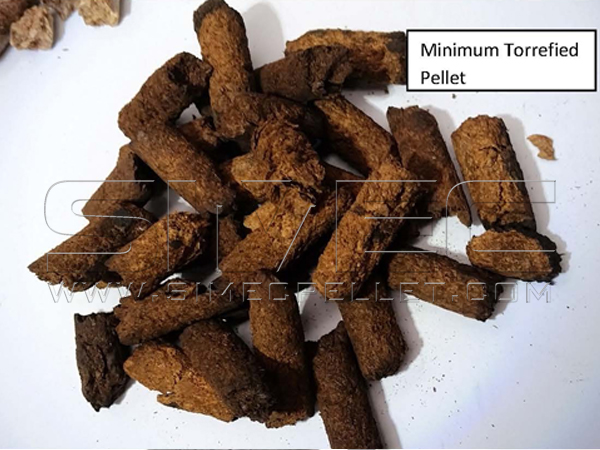
Minimun Torrefied Pellet
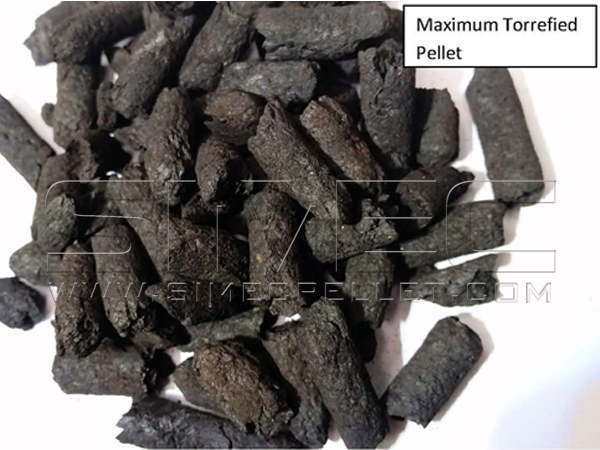
Maximum Torrefied Pellet
Once the material comes to the end of the reactor, it is transferred into a lock hopper receiving chamber ready to be loaded into the lock hopper, then the material is transferred into the cooling system, at last conveyed to a storage hopper ready to be shipped to the next process.
This system has the capability to vary the 3 main efficiency determining constraints required for optimum torrefaction, the controls allow for predetermined setups to suit different materials and have the capability to change performance during production as the feed of biomass may change.
The gases that exit the reactor are scrubber cleaned, cooled in readiness and sent to a distribution manifold. This distribution manifold will send gas back to the reactor heating burners as a priority so as the system is self-running, the next fraction of gas can be sent to the gas engine connected to an electricity generator, any remaining gas may be either interim stored further use or sent to the flue to be flared. It must be understood that the syngas produced will vary greatly with the quality of the biomass feedstock.
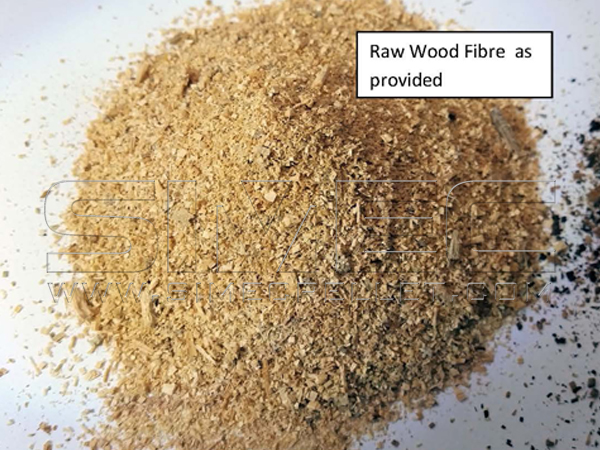
Raw Wood Fibre as Provided
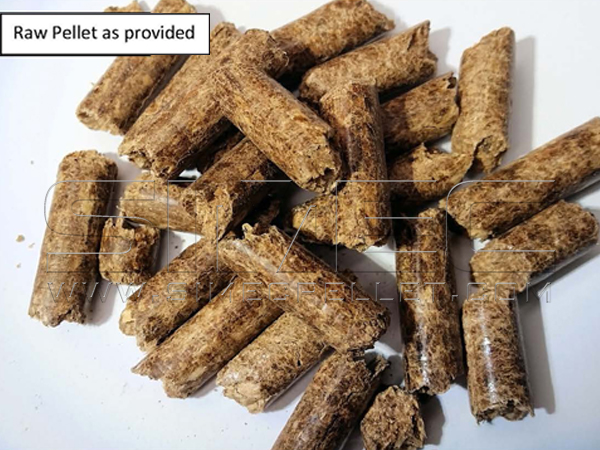
Raw Pellet as Provided
The prepared and sized material is fed from the hoppers to the Torrefaction system where the reactor process follows a closed loop control program that can vary the amount of gas to char production based on the energy requirement.
A basic summary of the Torrefaction system is described as:
The biomass material is fed into a preheat/drying chamber and transported through a low temperature zone, where the free water of the material can be dried off. Meanwhile, as the material temperature increasing in this chamber, the oxygen content of the ambient air will reduce.
Having passed through this stage, the material is then loaded into a lock hopper, where once the material is filled, the entry will be closed and the exit be opened. When the material is unloaded, the exit is closed, the entry opened and the loading cycle repeats. Once the material is inside the reactor chamber, the temperature and the internal pressure increase, and the ambient air is now at nearly zero oxygen. Any oxygen available is burned out with little effect to the large percentage of biomass in the reactor. As the material passes through the reactor, it is undergoing a change to its molecular state. When temperature is up to 100⁰C, any bound water is dried off and the particles dried out. At 200-400⁰C molecules of biomass decompose into solid and liquid yield along with non-condensable gases. This is called “Primary Torrefaction” and it occurs further down the reactor. Then the material travels further in the reactor, vapours are extracted and condensed as “tar” or “bio-oil”, while large molecules continue to be cracked yielding char at 300-500⁰C. This is called “Secondary Torrefaction”.
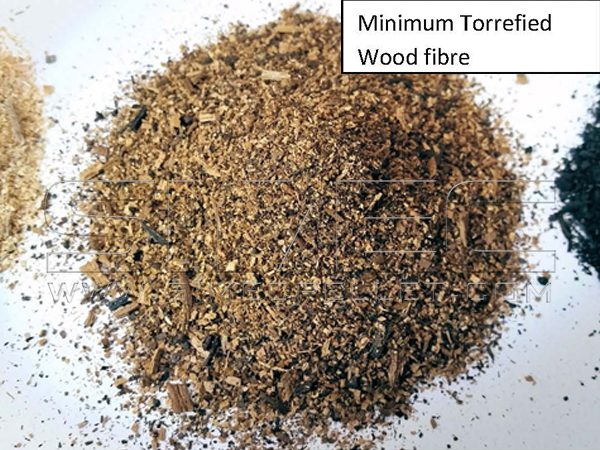
Minimum Torrefied Wood Fibre
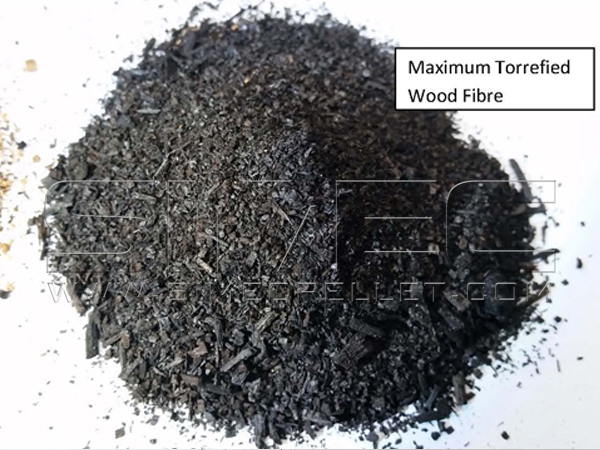
Maximum Torrefied Wood Fibre
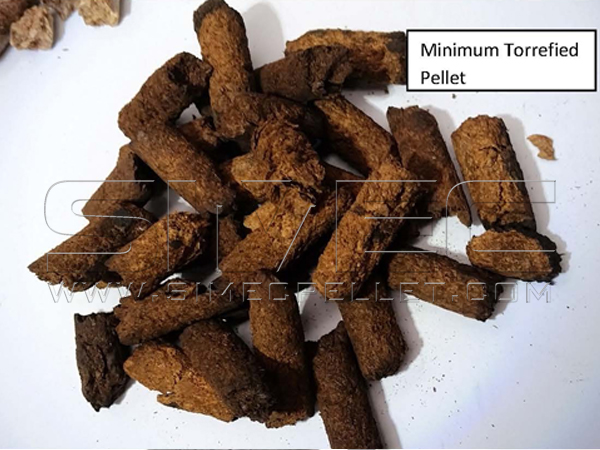
Minimun Torrefied Pellet
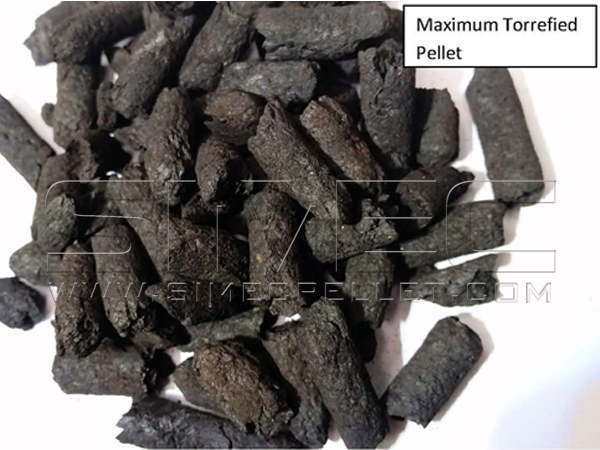
Maximum Torrefied Pellet
Once the material comes to the end of the reactor, it is transferred into a lock hopper receiving chamber ready to be loaded into the lock hopper, then the material is transferred into the cooling system, at last conveyed to a storage hopper ready to be shipped to the next process.
This system has the capability to vary the 3 main efficiency determining constraints required for optimum torrefaction, the controls allow for predetermined setups to suit different materials and have the capability to change performance during production as the feed of biomass may change.
The gases that exit the reactor are scrubber cleaned, cooled in readiness and sent to a distribution manifold. This distribution manifold will send gas back to the reactor heating burners as a priority so as the system is self-running, the next fraction of gas can be sent to the gas engine connected to an electricity generator, any remaining gas may be either interim stored further use or sent to the flue to be flared. It must be understood that the syngas produced will vary greatly with the quality of the biomass feedstock.
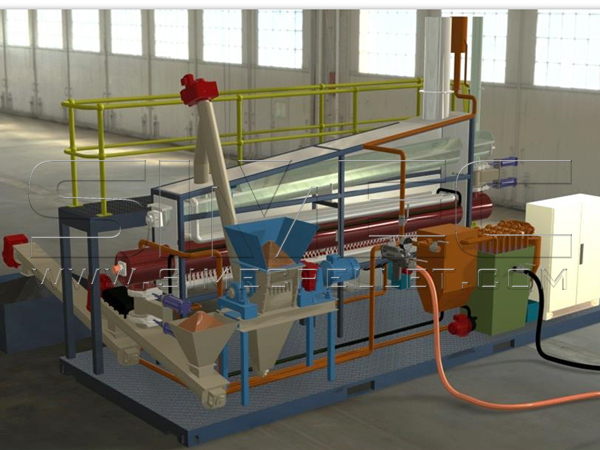
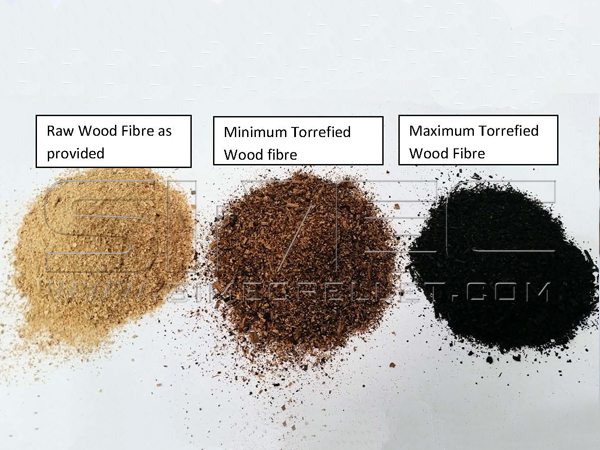
Wood Fibre Comparision
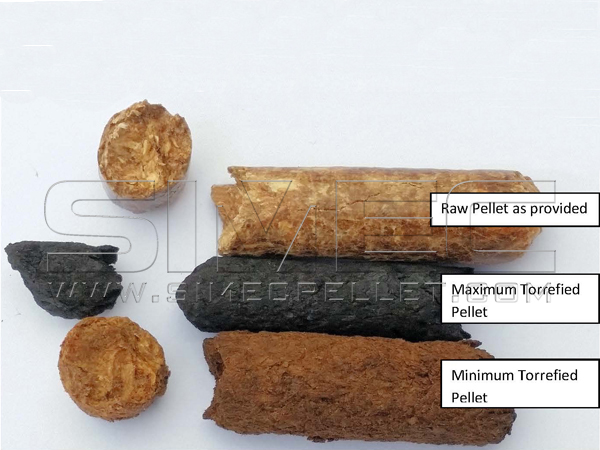
Pellet Comparision
We hope SIMEC technology and machinery will be helpful with your business development. Any question please feel free to contact us.