Integration of Counter-flow Pellet Cooler And Sieve
I. Application
Model SKLN14x14 counter-flow cooler is suitable for cooling the wood pellets after granulating in wood pellet factories, pellets coming out of the granulator are with high temperature, cooler can cooled down the pellets in a short time so as to assure continuously production of the whole flow-line, and making pellets easy to be stored, managed and transported.
SKLN14x14 counter-flow cooler is an integration of cooler and sievie, saving the floor space as well as the processing time.
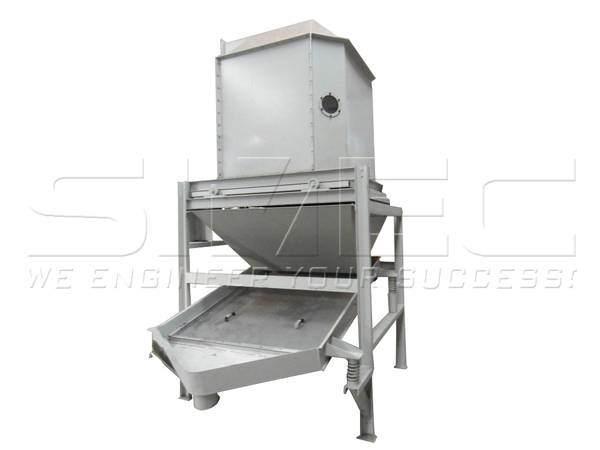
SKLN14x14 Integrated Pellet Cooler & Sifter
II. Working principles:
The machine consists of frame, feeding airlock, storage bin, discharging system, vibrating classifying sieve etc. While the machine starts to work, the high temperature pellets coming out of the granulating enter into the storage bin. The cool air enters into the storage bin through the bottom of the discharge device, rises upwards and is discharged through the air outlet. During rising, the cool air touches hot pellets and cools it. When the material layer reaches feed level-sensing device (NO.8), the discharge starts to discharge automatically, and when the material layer lowers to discharge level-sensing device (NO. 9), the discharger stops discharging automatically. The pellets dropping from the discharge device should be shaked to get powdery lot away, and after being discharged through the laying-off opening, it can be packed and weighed.
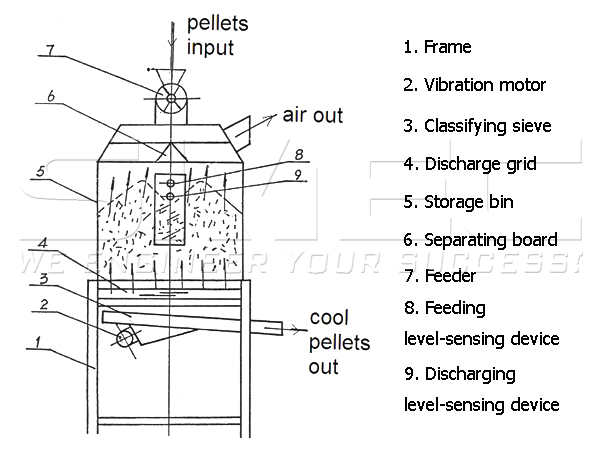
SKLN14x14 Integrated Pellet Cooler & Sifter Diagram
III. Parameter
Model SKLN14x14 counter-flow cooler is suitable for cooling the wood pellets after granulating in wood pellet factories, pellets coming out of the granulator are with high temperature, cooler can cooled down the pellets in a short time so as to assure continuously production of the whole flow-line, and making pellets easy to be stored, managed and transported.
SKLN14x14 counter-flow cooler is an integration of cooler and sievie, saving the floor space as well as the processing time.
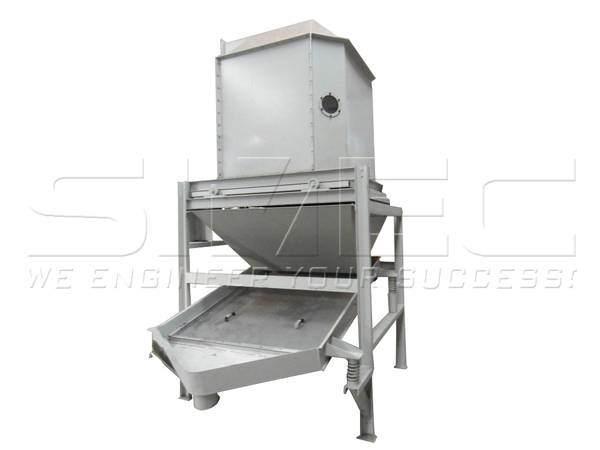
SKLN14x14 Integrated Pellet Cooler & Sifter
II. Working principles:
The machine consists of frame, feeding airlock, storage bin, discharging system, vibrating classifying sieve etc. While the machine starts to work, the high temperature pellets coming out of the granulating enter into the storage bin. The cool air enters into the storage bin through the bottom of the discharge device, rises upwards and is discharged through the air outlet. During rising, the cool air touches hot pellets and cools it. When the material layer reaches feed level-sensing device (NO.8), the discharge starts to discharge automatically, and when the material layer lowers to discharge level-sensing device (NO. 9), the discharger stops discharging automatically. The pellets dropping from the discharge device should be shaked to get powdery lot away, and after being discharged through the laying-off opening, it can be packed and weighed.
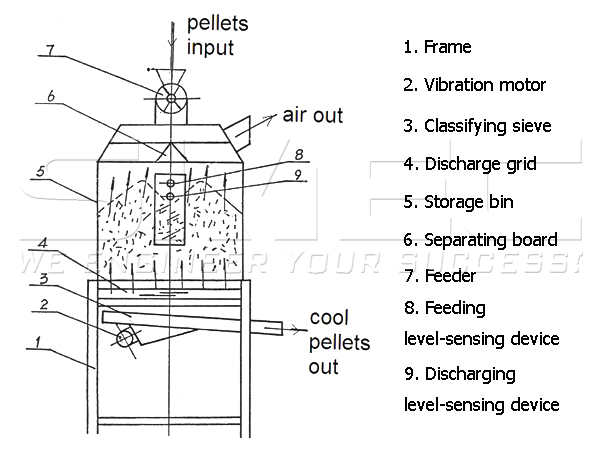
SKLN14x14 Integrated Pellet Cooler & Sifter Diagram
III. Parameter
Model | SKLN11×11 | SKLN14×14 | SKLN19×19 |
Temperature after cooling | Not higher than room temperature 5℃ | ||
Power(kW) | 2.2 | 3 | 3 |
IV. Characteristics
1. Low energy consumption.
In the counter-flow cooler, the cool air passes through material layer in vertical direction from the bottom (see figure 1). The newly absorbed air firstly touches cold pellet at the bottom and then hot pellet on the top through material pole. In the end, the temperature of the air coolant discharged almost equals its temperature at the feed opening, that is to say, the air can carry out the most heat quantity. It needs a small amount of air coolant, so the blower fan with less power can be use.
2. Even cooling.
Because the air coolant enters from the bottom of the whole cooler, rises through material layers slowly and evenly and then is discharged, there is little temperature difference in the same material layer.
3. Good pellet quality.
Pellets touch with the cool air which enters from the bottom shall be cooled down. The air is heated slowly while rising, and when it arrives on the top, it touches hot air heated beforehand, i.e. the temperature difference between all pellets layers and the air coolant decreases lest, avoiding such damages as cracks and cracking caused by shock cooling, which improves the quality of finished pellets.
4. No condensation or dew.
In the counter-flow cooler, because the air is heated intensively and the air temperature is kept over the moistening point in the cooling procedure, the dew won’t appear.
V. Installation drawings
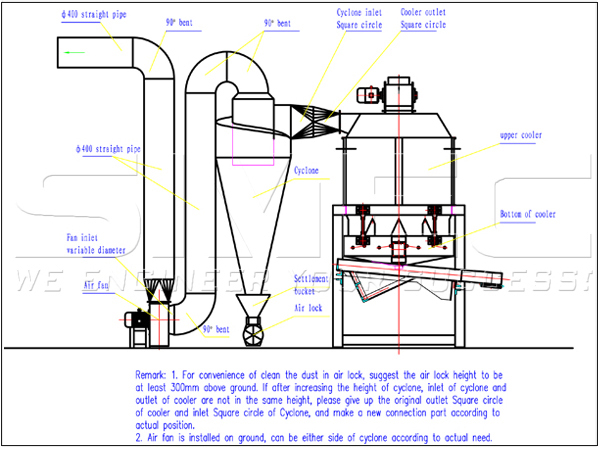
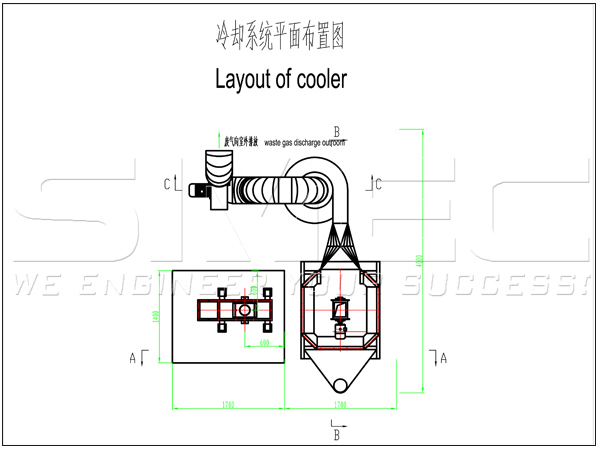
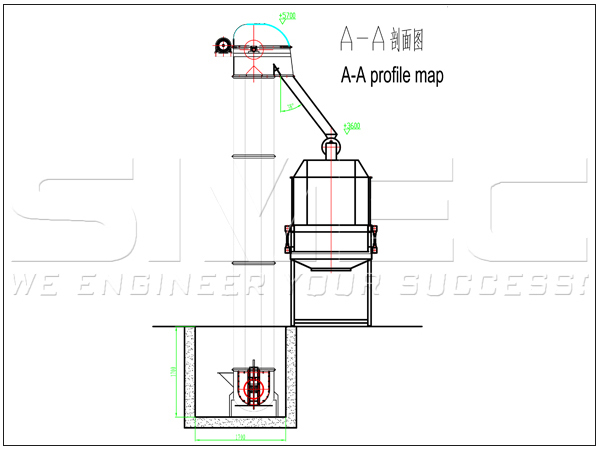
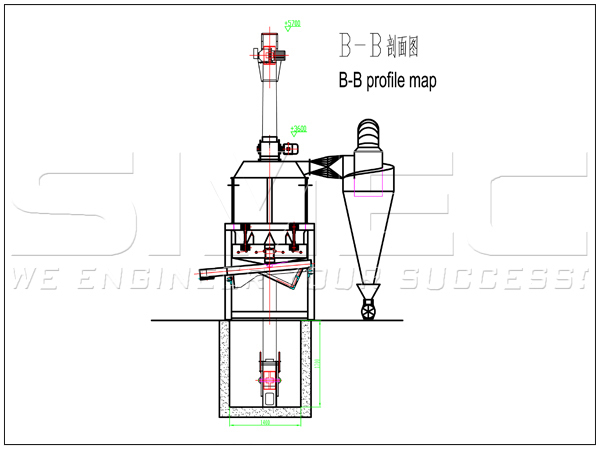
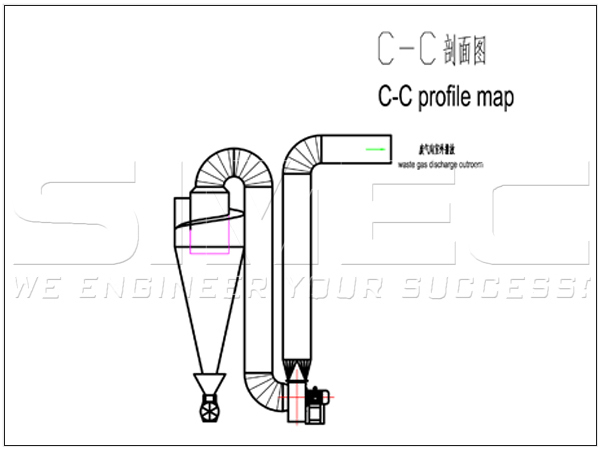